A precision control method for ultra-flat and ultra-thin precision strip steel roll system for backlight panels
A technology of roll system and configuration method, applied in manufacturing tools, metal rolling, metal rolling, etc., can solve problems such as restricting the flatness of ultra-flat precision stainless steel products, high requirements for roll system configuration, and large deformation of rolling mill stands. , to solve the production bottleneck, stabilize the surface quality, and improve the product quality.
- Summary
- Abstract
- Description
- Claims
- Application Information
AI Technical Summary
Problems solved by technology
Method used
Image
Examples
Embodiment 1
[0057] In this embodiment, Sundewei four-column 20-high rolling mill is used. According to the production plate shape, the roll system that the rolling mill needs to be equipped with is: the diameter of the backup roll is 165mm, the driving roll of the second intermediate roll is a flat roll, and the free roll of the second intermediate roll The convexity is 0.2 mm, the taper of the first intermediate roll is 130×0.2 mm, and the working roll is a flat roll.
[0058] The equipment process of the roll train of the rolling mill of the present embodiment is as follows:
[0059] Select a 165mm backing bearing for assembly, first measure the runout value of the bearing, and the runout value is within 0.005mm.
[0060] The bearing diameters are arranged according to the backing bearing diameter as follows:
[0061]
[0062] Measure the middle of the driving roll of the second intermediate roll, the double 1 / 4 side and the two ends of the roll, numbered 1-5, and ensure that the di...
Embodiment 2
[0072] In this embodiment, stainless steel with a steel grade of SUS316L, a thickness of 0.15 mm, and a width of 510 m is selected as a raw material. Select the 165mm support roll, driving roll, free roll with a crown of 0.2mm, the first intermediate roll of 130×0.2mm, and the work roll that has been ground according to the precision requirements. Roll trains are assembled for rolling.
[0073] The rolling table is as follows:
[0074]
[0075] During the rolling process, the shape control is fully automatic, and the work rolls are replaced every two passes. The finished product pass is tested for rolling, and after the rolled plate shape is stable, stop the car to take a sample with a length of 1m, and observe the warpage of the steel strip. After inspection, the warpage of the steel plate is less than 5cm, and the wave height is less than 3IU. Continue rolling until the rolling is completed.
PUM
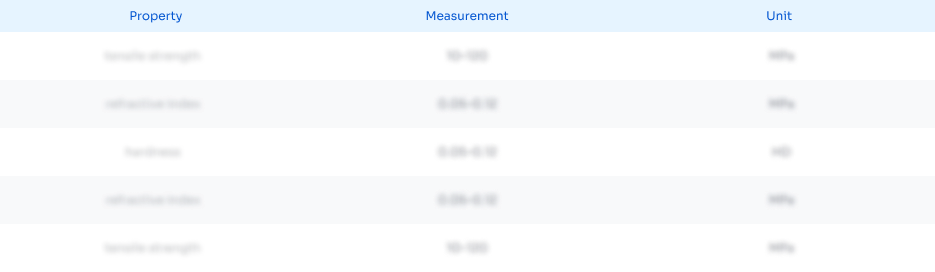
Abstract
Description
Claims
Application Information

- R&D
- Intellectual Property
- Life Sciences
- Materials
- Tech Scout
- Unparalleled Data Quality
- Higher Quality Content
- 60% Fewer Hallucinations
Browse by: Latest US Patents, China's latest patents, Technical Efficacy Thesaurus, Application Domain, Technology Topic, Popular Technical Reports.
© 2025 PatSnap. All rights reserved.Legal|Privacy policy|Modern Slavery Act Transparency Statement|Sitemap|About US| Contact US: help@patsnap.com