Real-time deformation monitoring method and system for frame section of tunnel shield tunneling machine under construction
A shield locomotive and deformation monitoring technology, applied in signal transmission systems, measuring devices, surveying and navigation, etc., can solve problems such as difficulty in erecting instruments, inability to continuously deform, and inability to monitor segments, and achieve high measurement accuracy and use. Safe and convenient effects
- Summary
- Abstract
- Description
- Claims
- Application Information
AI Technical Summary
Problems solved by technology
Method used
Image
Examples
Embodiment Construction
[0023] The present invention will be described in further detail below in conjunction with the accompanying drawings.
[0024] According to one or more embodiments, a real-time deformation monitoring system for the frame section of a shield machine under construction is disclosed, such as figure 1 As shown, it includes a light target and a test camera group. Along the traveling direction of the shield machine in the tunnel, the reference light target, the test camera group and the monitoring light target are arranged alternately in sequence. The light target and the test camera are fixed and installed. On the shield tunnel lining segments, they are arranged at intervals along the traveling direction of the shield machine. It also includes a wireless module installed on the test camera group and the light target for wireless communication, and a calculation system that receives data transmitted by the wireless module for calculation.
[0025] Such as figure 2 As shown, it is...
PUM
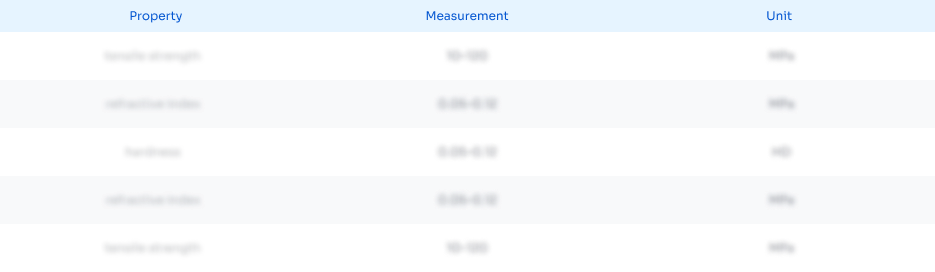
Abstract
Description
Claims
Application Information

- R&D
- Intellectual Property
- Life Sciences
- Materials
- Tech Scout
- Unparalleled Data Quality
- Higher Quality Content
- 60% Fewer Hallucinations
Browse by: Latest US Patents, China's latest patents, Technical Efficacy Thesaurus, Application Domain, Technology Topic, Popular Technical Reports.
© 2025 PatSnap. All rights reserved.Legal|Privacy policy|Modern Slavery Act Transparency Statement|Sitemap|About US| Contact US: help@patsnap.com