Special-shaped epoxy terrazzo wall surface embedded lamp strip profile and construction method thereof
An epoxy grinding stone, embedded technology, applied in the direction of floors, lighting devices, lighting and heating equipment, etc., can solve the problems of difficult replacement of light strips, high overall coverage repair costs, repair marks, etc., to achieve both functionality. And the effect of ornamental, convenient installation and saving construction cost
- Summary
- Abstract
- Description
- Claims
- Application Information
AI Technical Summary
Problems solved by technology
Method used
Image
Examples
Embodiment 1
[0035] From Figure 1-4 It can be seen that a special-shaped epoxy grindstone wall embedded lamp strip profile in this embodiment includes a reflective arc surface lamp groove 1, and a lamp groove closing cover plate is inserted into the upper part of the reflective arc surface lamp groove 1 2. The inner surface of the reflective curved lamp trough 1 is provided with a first card edge 11 , and the inclined soft strip light strip 3 is arranged on the first card edge 11 .
[0036] The first clamping edge 11 is arranged on the edge contact surface between the reflective curved light groove 1 and the inclined flexible light strip 3 , and the first clamping edge 11 extends outward by 3 mm for fixing the inclined flexible light strip 3 .
[0037] The reflective arc light trough 1 profile is 3mm thick, 48mm deep, and 58mm wide. There is a U-shaped card slot 12 at the connection between the reflective arc light trough 1 and the closing cover plate 2 of the light trough, and the U-shap...
PUM
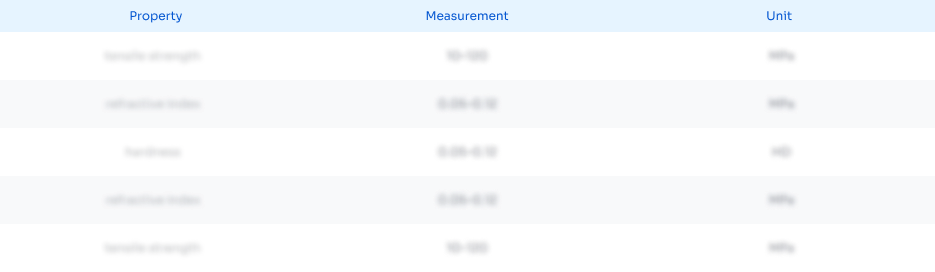
Abstract
Description
Claims
Application Information

- R&D Engineer
- R&D Manager
- IP Professional
- Industry Leading Data Capabilities
- Powerful AI technology
- Patent DNA Extraction
Browse by: Latest US Patents, China's latest patents, Technical Efficacy Thesaurus, Application Domain, Technology Topic, Popular Technical Reports.
© 2024 PatSnap. All rights reserved.Legal|Privacy policy|Modern Slavery Act Transparency Statement|Sitemap|About US| Contact US: help@patsnap.com