Aviation piston engine ground test bed system
A technology of piston engine and test bench, which is applied in engine testing, machine/structural component testing, measuring devices, etc., can solve the problems of test bench dumping, high temperature environment, and test bench structural damage, etc., to ensure accuracy, Improve the effectiveness of detection results
- Summary
- Abstract
- Description
- Claims
- Application Information
AI Technical Summary
Problems solved by technology
Method used
Image
Examples
no. 1 example
[0026] like figure 1 and figure 2 As shown, an aviation piston engine ground test platform system includes a base 1, the top of the base 1 is provided with a baffle 2, the baffle 2 is located at the back of the middle of the base 1, and the top of the base 1 is respectively provided with a front bracket 4 and a rear bracket 5. A beam 35 is provided between the front bracket 4 and the rear bracket 5. The beam 35 is used to ensure the stability between the front bracket 4 and the rear bracket 5. The front bracket 4 is located at the end of the rear bracket 5 away from the baffle 2. The rear bracket 5. A buffer bellows 19 is provided at the top, and the top of the buffer bellows 19 is provided with an engine 10. The buffer bellows 19 shocks and buffers the engine 10 during use to ensure the stability of the engine 10 during the test run. The top of the engine 10 is provided with The connecting belt 15 is used for bolt pulling the top of the engine 10 to ensure the stability of ...
no. 2 example
[0036] like Figure 3-7 The shown ground test platform system for aero piston engine, in actual use, when the air speed of the engine 10 decreases, the wind speed generated by the propeller 11 on one side of the engine 10 decreases, so that the engine 10 will be pulled down under the action of its own weight. The belt 15 is connected, and when the wind speed generated by the propeller 11 on the side of the engine 10 increases, the propeller 11 end of the engine 10 will rise upward to cause the base 1 or the baffle 2 to overturn, and at the same time, the engine 10 will generate heat when it is working. It is ensured that the base 1 and the baffle 2 will not be damaged when the airspeed of the engine 10 changes during use, and the generated wind can be prevented from being discharged at will, causing environmental pollution and damage, and improving the performance of the engine 10 and the base 1 and baffle 2. Cooling effect, the aero-piston engine ground test platform system a...
no. 3 example
[0052] It can be seen from the second embodiment that in actual use, the engine 10 will vibrate when it is working, and the buffer bellows 19 will have a good shock-absorbing and buffering effect on the vibration of the engine 10. The gas will be squeezed and expanded synchronously with the vibration of the engine 10, and when the engine 10 vibrates, it will also drive the vibration of the base 1, thereby causing damage to the operator and the top device. In order to solve the above problems, ensure that when the engine 10 vibrates Each part is still in an absolutely stable state. When the aviation piston engine ground test platform system is actually used: due to the relative distribution of the second air passage 18 and the third air passage 23, the air inlet 16 and the first air passage 17 are directly distributed. , so when each device is in a stable state and the engine 10 is working stably, the engine 10 will move downward due to its internal turbine structure. 19 exerts...
PUM
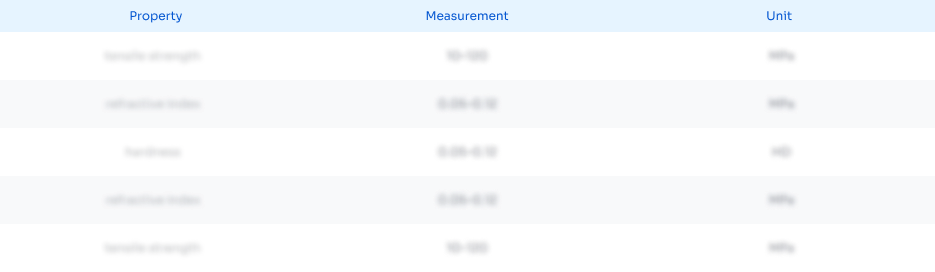
Abstract
Description
Claims
Application Information

- Generate Ideas
- Intellectual Property
- Life Sciences
- Materials
- Tech Scout
- Unparalleled Data Quality
- Higher Quality Content
- 60% Fewer Hallucinations
Browse by: Latest US Patents, China's latest patents, Technical Efficacy Thesaurus, Application Domain, Technology Topic, Popular Technical Reports.
© 2025 PatSnap. All rights reserved.Legal|Privacy policy|Modern Slavery Act Transparency Statement|Sitemap|About US| Contact US: help@patsnap.com