Method for preparing poly-alpha-olefin high-molecular polymer from coal-to-olefin and application of poly-alpha-olefin high-molecular polymer
A high-molecular polymer and coal-to-olefin technology, which is applied in the fields of hydrocarbon oil treatment, gas/liquid distribution and storage, and only multi-stage series refining process treatment, can solve the problems of molecular chain breakage and molecular weight reduction, and achieve anti-corrosion The effect of improving shear performance
- Summary
- Abstract
- Description
- Claims
- Application Information
AI Technical Summary
Problems solved by technology
Method used
Examples
Embodiment 1
[0021] Example 1 A kind of polyalpha-olefin polymer produced by coal-to-olefin
[0022] The preparation method is as follows:
[0023] 1. Mixture of C8α-olefins and alkanes:
[0024] Rectification: The coal-to-olefins containing a mixture of C6~C14α-olefins and alkanes are passed through the rectification tower (Shanghai Dayou DYH251 sieve tray tower) at a flow rate of 8L / h, the temperature of the tower is controlled at 70°C, and the top of the tower is heated at 2L / h. The h flow rate is the cut of C8 that carbon number is 8 through outlet rectification;
[0025] Refining: The C8 fraction obtained by rectification flows through the reactor equipped with catalyst alumina at a flow rate of 1L / h (the alumina is placed in the reactor in the form of a fixed bed), and the temperature of the reactor is controlled at 220°C for chemical reaction , after removing oxygen-containing compounds, a refined mixture of C8 α-olefins and alkanes with a carbon number of 8 is obtained.
[0026]...
Embodiment 2
[0033] Example 2 A kind of polyalpha-olefin polymer produced by coal-to-olefin
[0034] The preparation method is as follows:
[0035] 1. Mixture of C6α-olefins and alkanes:
[0036] Rectification: The coal-to-olefins containing a mixture of C6~C14α-olefins and alkanes are passed through the rectification tower (Shanghai Dayou DYH251 sieve tray tower) at a flow rate of 8L / h, the temperature of the tower is controlled at 30°C, and the top of the tower is heated at 2L / h. The h flow rate is the cut of C6 that carbon number is 6 through outlet rectification;
[0037] Refining: The C6 fraction obtained by rectification flows through the reactor equipped with catalyst alumina at a flow rate of 1L / h (alumina is placed in the reactor in the form of a fixed bed), and the temperature of the reactor is controlled at 220°C for chemical reaction , after removing oxygen-containing compounds, a refined mixture of C6α-olefins and alkanes with a carbon number of 6 is obtained.
[0038] 2. C...
Embodiment 3
[0043] Example 3 A kind of polyalpha-olefin polymer produced by coal-to-olefin
[0044] The preparation method is as follows:
[0045] 1. Mixture of C7α-olefins and alkanes:
[0046] Rectification: The coal-to-olefins containing a mixture of C6-C14α-olefins and alkanes are passed through the rectification tower (Shanghai Dayou DYH251 sieve tray tower) at a flow rate of 8L / h. h flow rate is the cut of C7 that carbon number is 7 through outlet rectification;
[0047] Refining: The C7 fraction obtained by rectification flows through a reactor equipped with catalyst alumina at a flow rate of 1L / h (alumina is placed in the reactor in the form of a fixed bed), and the temperature of the reactor is controlled at 230°C for chemical reaction , after removing oxygen-containing compounds, a refined mixture of C7α-olefins and alkanes with a carbon number of 7 is obtained.
[0048] 2. C9 α-olefin and alkane mixture: the method is the same as in Example 1.
[0049] 3. Mixture of C13α-ol...
PUM
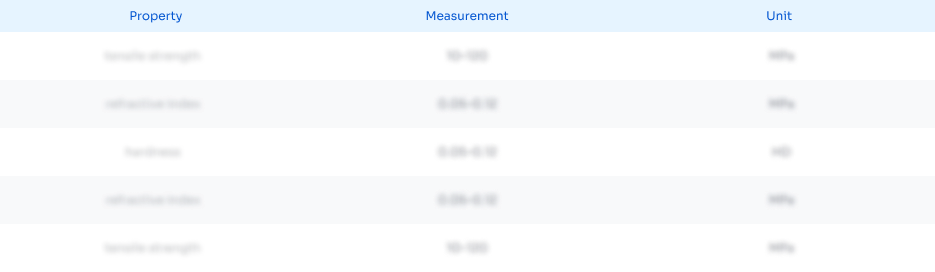
Abstract
Description
Claims
Application Information

- R&D
- Intellectual Property
- Life Sciences
- Materials
- Tech Scout
- Unparalleled Data Quality
- Higher Quality Content
- 60% Fewer Hallucinations
Browse by: Latest US Patents, China's latest patents, Technical Efficacy Thesaurus, Application Domain, Technology Topic, Popular Technical Reports.
© 2025 PatSnap. All rights reserved.Legal|Privacy policy|Modern Slavery Act Transparency Statement|Sitemap|About US| Contact US: help@patsnap.com