Machining method for large-size thin-wall special-shaped cover body
A processing method and large-scale technology, which are applied in the field of processing large-scale thin-walled special-shaped hoods, to achieve the effects of ensuring profile processing and testing accuracy, meeting cutting processing requirements, and high positioning accuracy
- Summary
- Abstract
- Description
- Claims
- Application Information
AI Technical Summary
Problems solved by technology
Method used
Image
Examples
Embodiment 1
[0041] In this embodiment, a large-sized thin-walled special-shaped ceramic cover has a blank length of about 1270 mm, a wall thickness of 6 mm, and a non-axisymmetric shape. The following is the specific process of processing method implementation:
[0042] Step (1), design and manufacture special tooling for cutting processing, including fast flexible clamping device on the outer surface and flexible support on the inner surface, reversible quick positioning device, to meet the requirements of fast clamping, adjustable clamping position, quick positioning by flipping, etc. Features.
[0043]Step (2), put the product blank into the tooling. After the blank is scanned, 3D reverse modeling is carried out, and the blank digital model is compared with the product digital model to determine the position of the product relative to the blank. Through the relative positional relationship between the blank and the product digital model, the blank is clamped and fixed on the tooling. ...
PUM
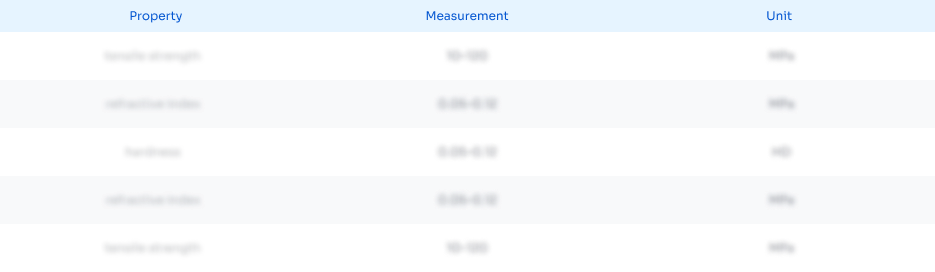
Abstract
Description
Claims
Application Information

- Generate Ideas
- Intellectual Property
- Life Sciences
- Materials
- Tech Scout
- Unparalleled Data Quality
- Higher Quality Content
- 60% Fewer Hallucinations
Browse by: Latest US Patents, China's latest patents, Technical Efficacy Thesaurus, Application Domain, Technology Topic, Popular Technical Reports.
© 2025 PatSnap. All rights reserved.Legal|Privacy policy|Modern Slavery Act Transparency Statement|Sitemap|About US| Contact US: help@patsnap.com