Inspection robot
A technology for inspection robots and casings, applied in the field of inspection robots, can solve problems such as time-consuming, difficult for tunnel managers, and difficult to be understood, so as to improve comprehensiveness and accuracy, avoid mutual influence, and improve movement ability Effect
- Summary
- Abstract
- Description
- Claims
- Application Information
AI Technical Summary
Problems solved by technology
Method used
Image
Examples
Embodiment Construction
[0038] In order to make the object, technical solution and advantages of the present invention clearer, the present invention will be further described in detail below in conjunction with the accompanying drawings and embodiments. It should be understood that the specific embodiments described here are only used to explain the present invention, and are not intended to limit the present invention.
[0039] An inspection robot, which includes an attachment mechanism, a detection structure, a motion mechanism, a radio communication mechanism, an evacuation mechanism, a heat dissipation mechanism and a fuselage structure; as figure 1 , figure 2 As shown, the fuselage mechanism includes an upper casing (8), a lower casing (9), a front side plate (19), and a rear side plate (23), wherein the lower casing (8), the upper casing (9) It is the base frame for the inspection robot to install other parts. The infrared temperature sensor (10), laser ranging sensor (11), smoke sensor (12)...
PUM
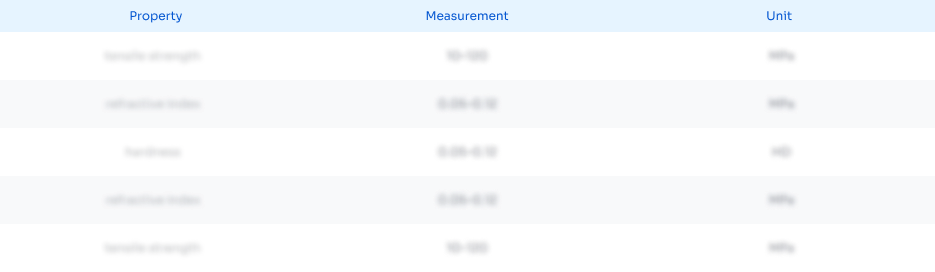
Abstract
Description
Claims
Application Information

- Generate Ideas
- Intellectual Property
- Life Sciences
- Materials
- Tech Scout
- Unparalleled Data Quality
- Higher Quality Content
- 60% Fewer Hallucinations
Browse by: Latest US Patents, China's latest patents, Technical Efficacy Thesaurus, Application Domain, Technology Topic, Popular Technical Reports.
© 2025 PatSnap. All rights reserved.Legal|Privacy policy|Modern Slavery Act Transparency Statement|Sitemap|About US| Contact US: help@patsnap.com