AGV attitude adjusting method applied to tray identification/positioning
A pallet and attitude technology, applied in the field of automated logistics, can solve the problems of pallet scanning, increase the difficulty of promotion, and increase the difficulty of workers' placement, and achieve the effect of ensuring accuracy, reducing costs and difficulty in software development.
- Summary
- Abstract
- Description
- Claims
- Application Information
AI Technical Summary
Problems solved by technology
Method used
Image
Examples
Embodiment 1
[0043] A method for adjusting the posture of an AGV applied to pallet recognition / positioning, comprising the following steps,
[0044] Step S1, move the AGV to the front point of the pallet;
[0045] Step S2, scanning the position and posture of the pallet through the 3D vision sensor, and transmitting the data to the controller;
[0046] Step S3, the controller receives the data, and controls the AGV body 1 to rotate in situ according to the angle deviation data of the pallet, and adjusts the direction of the AGV body 1 until the fork is perpendicular to the fork-in direction of the pallet;
[0047] Step S4, after the AGV body 1 is adjusted, the fork-in direction is completely perpendicular to the fork-in surface of the pallet, but at this time the center line of the pallet frame does not coincide with the vertical line in the fork-in direction of the pallet, so the 3D vision sensor scans again and transmits the data to the controller;
[0048] Step S5, the controller rece...
Embodiment 2
[0053] Said step S3 comprises the following steps,
[0054] Step S31, the controller receives the data obtained by scanning the position and attitude of the pallet through the 3D vision sensor 3 in step S2;
[0055] Step S32, controlling the AGV body 1 to rotate in situ according to the angle deviation data of the pallet;
[0056] In step S33, it is judged whether the AGV body 1 is perpendicular to the fork-in direction of the pallet, otherwise step S2 is performed again, and if so, step S4 is performed.
[0057]On the basis of Embodiment 1, the AGV body 1 is rotated in situ, and the direction of the AGV body 1 is adjusted, that is, the width of the roadway is lower. At the same time, judgment logic is added during the rotation process to determine whether the AGV body 1 is Perpendicular to the fork-in direction of the pallet, the accuracy of the judgment is guaranteed through the judgment of the continuity of the cycle, but there may be certain errors in the actual operation...
Embodiment 3
[0059] Step S51, the controller receives the data obtained by scanning the tray again by the 3D vision sensor 3 in step S4;
[0060] Step S52, the controller receives the data, so as to translate the tray rack 2 in the horizontal direction according to the data;
[0061] Step S53, judging whether the center line of the tray rack 2 coincides with the center line of the tray in the fork-in direction, otherwise, go to step S4 again. If so, go to step S6.
[0062] On the basis of Example 1, the pallet rack 2 is translated left and right, only moving on the AGV car body 1, and there is no requirement for the width of the roadway. Whether the center line coincides, the accuracy of the judgment is guaranteed through the judgment of the continuity of the cycle, as described in Example 2, there may be certain errors in the actual operation process, and the error range can be adjusted according to the actual situation, such as adjusting the error range When it is -5mm~5mm, that is, whe...
PUM
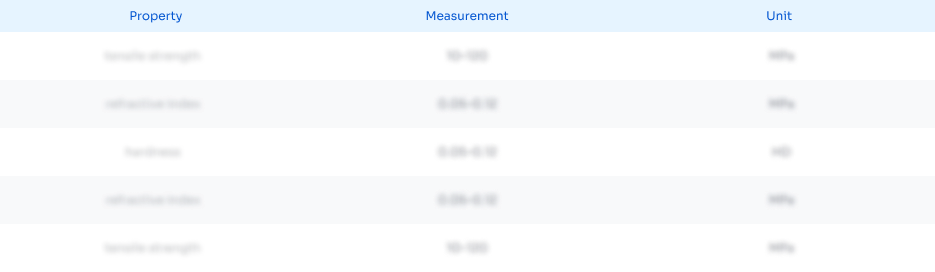
Abstract
Description
Claims
Application Information

- R&D
- Intellectual Property
- Life Sciences
- Materials
- Tech Scout
- Unparalleled Data Quality
- Higher Quality Content
- 60% Fewer Hallucinations
Browse by: Latest US Patents, China's latest patents, Technical Efficacy Thesaurus, Application Domain, Technology Topic, Popular Technical Reports.
© 2025 PatSnap. All rights reserved.Legal|Privacy policy|Modern Slavery Act Transparency Statement|Sitemap|About US| Contact US: help@patsnap.com