Collision-based low-frequency and multi-direction vibration energy collecting device
A vibration energy collection and multi-directional technology, applied in electromechanical devices, electrical components, etc., can solve the problems of inability to efficiently capture low-frequency multi-directional vibration energy, high operating frequency, etc., achieve efficient energy conversion and improve the effect of up-frequency
- Summary
- Abstract
- Description
- Claims
- Application Information
AI Technical Summary
Problems solved by technology
Method used
Image
Examples
Embodiment 1
[0023] A low-frequency, multi-directional vibration energy harvesting device based on collision, refer to Figures 1 to 4 , including a housing 3, a spring 2, an insulating support rod 8, a magnet 9, a coil 10, an annular barrier piece 7, a mass 4, and a rope 5; the upper surface of the housing 3 protrudes with a hard collision rod 11; the One end of the spring 2 is fixedly connected to the bottom of the housing 3, and the other end of the spring 2 is fixedly connected to the lower base 1; one end of the insulating support rod 8 is fixedly connected to the magnet 9, and the other end of the insulating support rod 8 It is fixedly connected with the lower base 1; the magnet 9 is fixed inside the housing 3 at a certain distance from the upper bottom surface of the housing 3; the end of the hard collision rod 11 away from the housing 3 is inserted into the inside of the blocking piece 7 One end of the mass block 4 is fixedly connected with the end of the blocking piece 7 facing aw...
PUM
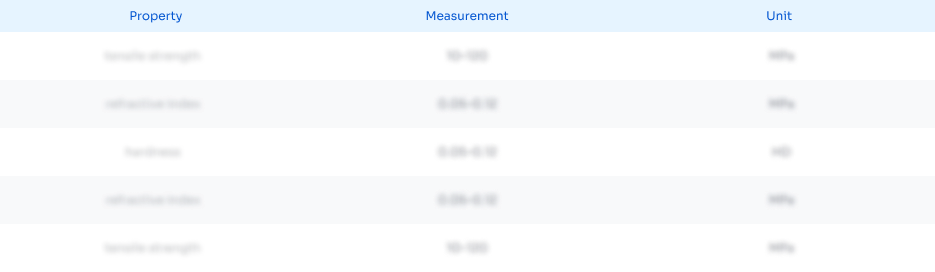
Abstract
Description
Claims
Application Information

- R&D Engineer
- R&D Manager
- IP Professional
- Industry Leading Data Capabilities
- Powerful AI technology
- Patent DNA Extraction
Browse by: Latest US Patents, China's latest patents, Technical Efficacy Thesaurus, Application Domain, Technology Topic, Popular Technical Reports.
© 2024 PatSnap. All rights reserved.Legal|Privacy policy|Modern Slavery Act Transparency Statement|Sitemap|About US| Contact US: help@patsnap.com