Preparation method and device of niobium-iron alloy
A niobium-iron alloy and preparation device technology, applied in the field of niobium-iron alloy, can solve the problems of easily generating large dust and affecting the health of the staff, and achieve the effects of preventing temperature drop, facilitating pick-and-place, and improving collection efficiency
- Summary
- Abstract
- Description
- Claims
- Application Information
AI Technical Summary
Problems solved by technology
Method used
Image
Examples
Embodiment 1
[0058] A method for preparing niobium-iron alloy. The niobium sputtering target is crushed, then ground into a powder with a particle size of 40-80 mesh, and oxidized at a certain temperature of 380 degrees for 4.5 hours. After oxidation, the niobium sputtering target powder, aluminum powder, and iron powder 1. Lime is mixed evenly according to the mass ratio of 1:0.69:0.59:0.1, loaded into the preparation device, and then ignited for reaction. During the reaction, electrodes are installed to supplement heat, and aluminum powder is added as a reducing agent. The temperature is lowered to room temperature, the charge is poured out, the slag and ferroniobium alloy are separated, and crushed respectively to obtain ferroniobium alloy products and high-aluminum ferroniobium slag.
Embodiment 2
[0060] A method for preparing niobium-iron alloys. The niobium sputtering target is crushed, then ground into a powder with a particle size of 40-80 mesh, and oxidized at a certain temperature of 400 degrees for 4 hours. After oxidation, the niobium sputtering target powder, aluminum powder, iron powder, The lime is mixed evenly according to the mass ratio of 1:0.69:0.59:0.1, loaded into the preparation device, and then ignited for reaction. During the reaction, electrodes are installed to supplement heat, and aluminum powder is added as a reducing agent. After fifteen minutes, the reaction is over and the furnace charge is naturally cooled. After reaching room temperature, pour out the charge, separate the slag and ferroniobium alloy, and crush them respectively to obtain ferroniobium alloy products and high-aluminum ferroniobium slag.
Embodiment 3
[0062] A method for preparing niobium-iron alloy. The niobium sputtering target is crushed, then ground into a powder with a particle size of 40-80 mesh, and oxidized at a certain temperature of 420 degrees for 3.5 hours. After oxidation, the niobium sputtering target powder, aluminum powder, and iron powder 1. Lime is mixed evenly according to the mass ratio of 1:0.69:0.59:0.1, loaded into the preparation device, and then ignited for reaction. During the reaction, electrodes are installed to supplement heat, and aluminum powder is added as a reducing agent. The temperature is lowered to room temperature, the charge is poured out, the slag and ferroniobium alloy are separated, and crushed respectively to obtain ferroniobium alloy products and high-aluminum ferroniobium slag.
[0063] Tested ferroniobium alloy products: Nb:60~70, Ta:0.5, Al:2.0, Si:0.4, C:0.04, S:0.02, P:0.02, W:0.2, Ti:0.2, Cu:0.3, Mn: 0.3, As: 0.005, Sn: 0.002, Sb: 0.002, Pb: 0.002, Bi: 0.002.
[0064] see ...
PUM
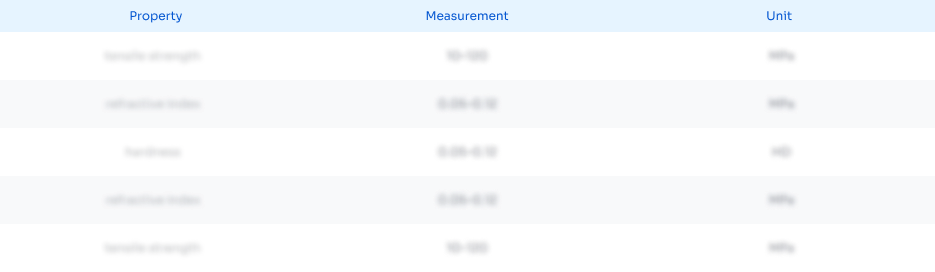
Abstract
Description
Claims
Application Information

- R&D
- Intellectual Property
- Life Sciences
- Materials
- Tech Scout
- Unparalleled Data Quality
- Higher Quality Content
- 60% Fewer Hallucinations
Browse by: Latest US Patents, China's latest patents, Technical Efficacy Thesaurus, Application Domain, Technology Topic, Popular Technical Reports.
© 2025 PatSnap. All rights reserved.Legal|Privacy policy|Modern Slavery Act Transparency Statement|Sitemap|About US| Contact US: help@patsnap.com