Ammonia distillation treatment process for residual ammonia water
A treatment process and ammonia water technology, which are applied in the field of residual ammonia water distillation and ammonia treatment process, can solve the problems of blockage of tar discharge pipes, high water output from circulating water, and high treatment costs, and achieve the effects of preventing low-temperature solidification, increasing service life and increasing operating time.
- Summary
- Abstract
- Description
- Claims
- Application Information
AI Technical Summary
Problems solved by technology
Method used
Image
Examples
Embodiment Construction
[0025] The present invention will be further described below in conjunction with the embodiments and accompanying drawings. The specific embodiments are only used to further describe the present invention in detail, and do not limit the protection scope of the claims of the present application.
[0026] The invention provides a process for distilling ammonia from residual ammonia water (referred to as process), which is characterized in that the process is as follows:
[0027]The remaining ammonia water (temperature is 60-75°C) comes from outside the boundary area; after entering the boundary area, it is divided into two feeds, and the first residual ammonia water feed enters the feed cooler 15 to cool down through circulating water, and then is fed by the ammonia distillation tower 1. Once the feed port at the top of the tower enters the tower; the second residual ammonia water feed passes through the feed preheater 6, and through the waste water pump 5, heats up with the was...
PUM
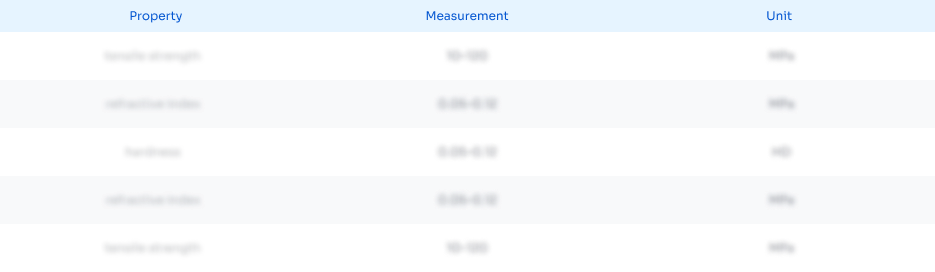
Abstract
Description
Claims
Application Information

- R&D
- Intellectual Property
- Life Sciences
- Materials
- Tech Scout
- Unparalleled Data Quality
- Higher Quality Content
- 60% Fewer Hallucinations
Browse by: Latest US Patents, China's latest patents, Technical Efficacy Thesaurus, Application Domain, Technology Topic, Popular Technical Reports.
© 2025 PatSnap. All rights reserved.Legal|Privacy policy|Modern Slavery Act Transparency Statement|Sitemap|About US| Contact US: help@patsnap.com