Hollow Fe2O3 coated carbon catalyst as well as preparation method and application thereof
A carbon catalyst, fe2o3 technology, applied in the direction of metal/metal oxide/metal hydroxide catalyst, physical/chemical process catalyst, chemical instrument and method, etc., can solve the problems of toxicity, human harm, etc. Catalytic performance, effect of large specific surface area
- Summary
- Abstract
- Description
- Claims
- Application Information
AI Technical Summary
Problems solved by technology
Method used
Image
Examples
Embodiment 1
[0028] Example 1 Hollow Fe 2 o 3 Preparation of Coated Carbon (MIL-88A+K) Catalyst
[0029] 1) Fe 2 o 3 Preparation of hollow microspheres: FeCl 3 ·6H2 O 4.56g, sodium citrate 9.6g, urea 1.65g were dissolved in 80ml of deionized water and stirred for 30min, then added 0.8g of polyvinylpyrrolidone (ie pvp) and continued to stir for 1h, then hydrothermally reacted at 100°C for 24h to obtain hollow Fe 2 o 3 Microspheres, Fe in the following examples 2 o 3 Hollow microsphere preparation method is with embodiment 1;
[0030] 2) 1g Fe 2 o 3 Hollow microspheres and 0.5804g C 4 h 4 o 4 Dissolve in 25mL deionized water, then add 1.3515g FeCl 3 ·6H 2 O was stirred until completely dissolved, washed by centrifugation, and dried at 80°C to obtain the product;
[0031] 3) Dissolve 4.05g of the product in step 2) in 120mL of 1M glucose solution, heat it in water at 180°C for 12h, wash the product by centrifugation and dry it at 80°C to obtain hollow Fe 2 o 3 Coated carbon c...
Embodiment 2
[0034] with hollow Fe 2 o 3 Coated carbon (MIL-88B) catalyst is an example, and its preparation method is as follows:
[0035] 1) Add 1gFe 2 o 3 Hollow microspheres and FeCl 3 ·6H 2 O (16mL 40mM) ethanol solution was mixed evenly at room temperature, and the solution was added terephthalic acid (16mL 20mM) ethanol solution in an ultrasonic device at 70°C, and after mixing evenly, it was centrifugally washed and dried at 80°C; In 120mL of 1M fructose solution, heated at 180°C for 12h, the obtained product was washed by centrifugation and dried at 80°C to obtain hollow Fe 2 o 3 Coating carbon catalyst precursors;
[0036] 2) The obtained hollow Fe 2 o 3 The coated carbon catalyst precursor was calcined at 450 °C (heating rate 1 °C / min) in air atmosphere for 5 hours to obtain the final product hollow Fe 2 o 3 Coated carbon (MIL-88B) catalyst.
Embodiment 3
[0038] Hollow Fe 2 o 3 The preparation method of coated carbon (MIL-100) catalyst is as follows:
[0039] 1) Add 1gFe 2 o 3 Hollow microspheres and FeCl 3 ·6H 2 O (16mL 40mM) ethanol solution was mixed evenly at room temperature, and the solution was added triformic acid (16mL 40mM) ethanol solution in a 70°C ultrasonic device, after mixing evenly, it was washed by centrifugation and dried at 80°C; 4.05g of the product from the previous step was dissolved in 120mL 1M sucrose solution, heated at 180°C for 12 hours, centrifuged, washed and dried at 80°C to obtain hollow Fe 2 o 3 Coating carbon catalyst precursors;
[0040] 2) Then obtain hollow Fe 2 o 3 Coated carbon catalyst precursor; the final product, hollow Fe 2 o 3 Coated carbon (MIL-101) catalyst.
PUM
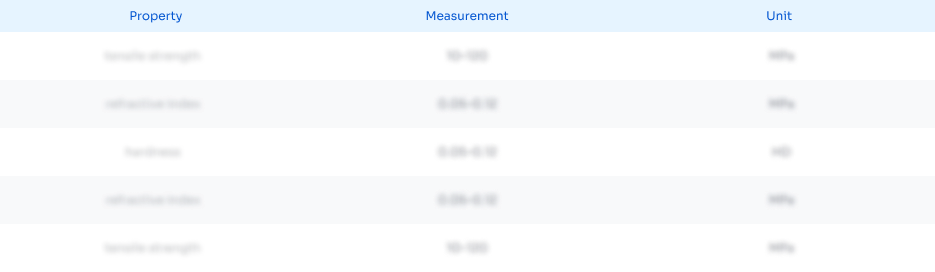
Abstract
Description
Claims
Application Information

- R&D
- Intellectual Property
- Life Sciences
- Materials
- Tech Scout
- Unparalleled Data Quality
- Higher Quality Content
- 60% Fewer Hallucinations
Browse by: Latest US Patents, China's latest patents, Technical Efficacy Thesaurus, Application Domain, Technology Topic, Popular Technical Reports.
© 2025 PatSnap. All rights reserved.Legal|Privacy policy|Modern Slavery Act Transparency Statement|Sitemap|About US| Contact US: help@patsnap.com