Online monitoring method for looseness of flange connecting bolt
A technology for connecting bolts and flanges, which is applied in the field of online monitoring of flange connection bolt loosening, can solve the problems of inability to effectively display the bolt loosening state and load state, and inability to effectively monitor tangential displacement, and achieve the effect of high monitoring sensitivity.
- Summary
- Abstract
- Description
- Claims
- Application Information
AI Technical Summary
Problems solved by technology
Method used
Image
Examples
Embodiment 1
[0049] refer to Figure 1 to Figure 9 , the invention provides a method for on-line monitoring of flange connection bolt looseness, comprising the following steps:
[0050] S1. Four displacement sensors 16 are evenly arranged on the inner or outer circumference of the flange connection;
[0051] The displacement sensor at least includes a housing 1, a limit block 2 and a sensing module located in the housing, which are used to monitor the displacement changes of the upper and lower flanges. Specifically, when the mounting surface of the limit block and the housing are on the same plane, The limit block and the housing are directly fixed on the two measured parts. When the mounting surfaces of the limit block and the housing are on different planes, the limit block and the housing are fixed on the two parts through the installation pad 3. on the component under test, such as figure 2 and Figure 4 As shown, by adjusting the thickness of the limit block or the mounting pad c...
Embodiment 2
[0080] The structure of the displacement sensor used in this embodiment is basically the same as that of Embodiment 1. The difference is that there is only one connecting rod in this embodiment, such as Figure 10 to Figure 11 As shown, at this time, there is a mounting hole on the limit block along the installation direction of the sensor. The mounting hole runs through the limit block. During the lateral relative displacement, the limit block drives the connecting rod to move laterally to the left or right, thereby driving the lateral sliding base to move. The surface of the mounting hole is smooth, so that when the upper and lower flanges are displaced longitudinally, the limiting block and the connecting rod move longitudinally relative to each other without affecting the lateral sliding base.
[0081] The present invention provides an on-line monitoring method for flange connection bolt looseness, which simultaneously considers the relative displacement along the axial di...
PUM
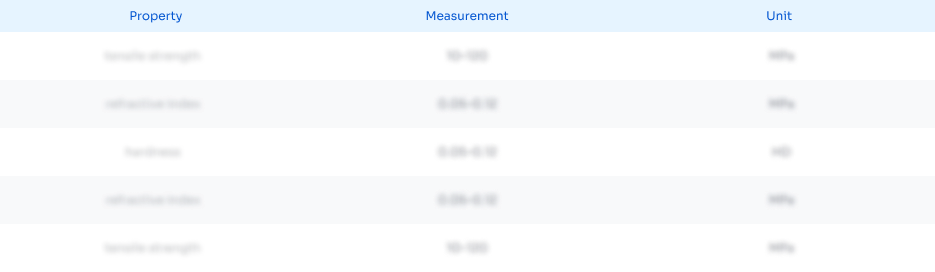
Abstract
Description
Claims
Application Information

- R&D
- Intellectual Property
- Life Sciences
- Materials
- Tech Scout
- Unparalleled Data Quality
- Higher Quality Content
- 60% Fewer Hallucinations
Browse by: Latest US Patents, China's latest patents, Technical Efficacy Thesaurus, Application Domain, Technology Topic, Popular Technical Reports.
© 2025 PatSnap. All rights reserved.Legal|Privacy policy|Modern Slavery Act Transparency Statement|Sitemap|About US| Contact US: help@patsnap.com