Outer duct casing based on chemical milling process
A technology of external ducting and chemical milling, which is applied in the direction of mechanical equipment, engine components, machines/engines, etc., can solve problems such as drawing reinforcement ribs, and the method of determining the integer coefficients of reinforcement units has not been introduced. The effect of reducing the difficulty of design
- Summary
- Abstract
- Description
- Claims
- Application Information
AI Technical Summary
Problems solved by technology
Method used
Image
Examples
Embodiment 1
[0033] Such as Figure 1 to Figure 8 The shown one based on the chemical milling process of the external channel casing, including the front casing and the rear casing 3, the front casing and the rear casing 3 have grid-like ribs, and the shape of the grid unit of the ribs is Triangular or quadrangular; the front casing is a cone-shaped shell structure, and the rear casing 3 is a cylindrical structure.
Embodiment 2
[0035] Based on embodiment 1, and the front receiver is divided into upper and lower parts, which are the upper part 1 of the front receiver and the lower part 2 of the front receiver respectively.
Embodiment 3
[0037] Based on embodiment 1, and the shape of the grid unit of the reinforcing rib on the front casing is a longitudinal triangle, and one side of the longitudinal triangular reinforcing rib must be parallel to the axial direction.
PUM
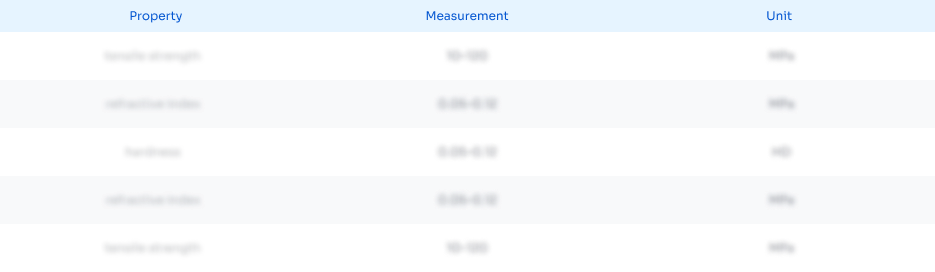
Abstract
Description
Claims
Application Information

- R&D Engineer
- R&D Manager
- IP Professional
- Industry Leading Data Capabilities
- Powerful AI technology
- Patent DNA Extraction
Browse by: Latest US Patents, China's latest patents, Technical Efficacy Thesaurus, Application Domain, Technology Topic, Popular Technical Reports.
© 2024 PatSnap. All rights reserved.Legal|Privacy policy|Modern Slavery Act Transparency Statement|Sitemap|About US| Contact US: help@patsnap.com