Milling machine fixture and clamping method for air fuel radiator core assembly
A milling machine fixture and radiator technology, which is applied in the field of mechanical processing, can solve the problems of non-adjustable auxiliary support force, deformation of component clamping and processing, and lack of auxiliary support points, etc., to achieve convenient adjustment and coordination of limit positions, and convenient positioning and clamping operations , The effect of convenient leveling process
- Summary
- Abstract
- Description
- Claims
- Application Information
AI Technical Summary
Problems solved by technology
Method used
Image
Examples
Embodiment Construction
[0053] The embodiments of the present invention will be further described below in conjunction with the accompanying drawings, but the protection scope of the claims of the present invention is not limited to the content listed in this embodiment.
[0054] In this embodiment, the milling machine fixture of the air-fuel radiator core assembly includes: a flange positioning plate 1, a mounting support 2, an adjusting screw 3, a positioning block 4, a pressing plate 5, and a connecting locking member 6, etc. See the views of the milling machine fixture for the air-fuel radiator core assembly Figure 1 to Figure 4 shown; the structural diagram of the air-fuel radiator core assembly is shown in Figure 5 , the sketch of the product with the core assembly on the fixture of the air-fuel radiator core assembly milling machine is shown in Figure 6 .
[0055] The functions and structural characteristics of each component in the milling machine fixture of the air-fuel radiator core ass...
PUM
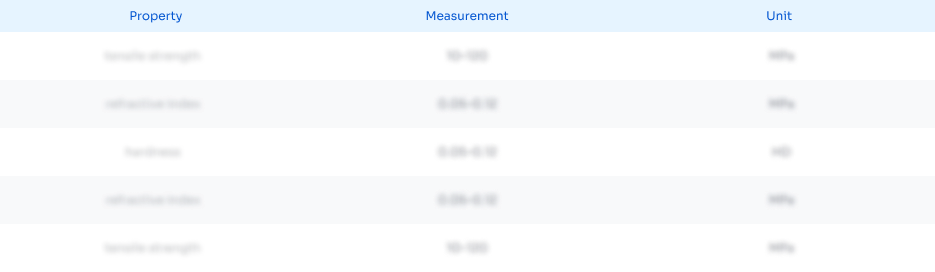
Abstract
Description
Claims
Application Information

- R&D
- Intellectual Property
- Life Sciences
- Materials
- Tech Scout
- Unparalleled Data Quality
- Higher Quality Content
- 60% Fewer Hallucinations
Browse by: Latest US Patents, China's latest patents, Technical Efficacy Thesaurus, Application Domain, Technology Topic, Popular Technical Reports.
© 2025 PatSnap. All rights reserved.Legal|Privacy policy|Modern Slavery Act Transparency Statement|Sitemap|About US| Contact US: help@patsnap.com