Powder filling machine
A filling machine and powder technology, applied in the direction of solid materials, packaging, packaging items, etc., can solve the problem of slow filling speed, and achieve the effect of improving fluidity, facilitating internal cleaning, and improving filling speed.
- Summary
- Abstract
- Description
- Claims
- Application Information
AI Technical Summary
Problems solved by technology
Method used
Image
Examples
specific Embodiment 1
[0048] Such as Figure 1 to Figure 7 As shown, in the powder filling machine provided in this embodiment, a filling pipe 9 is provided at the outlet of the front end of the conveying cylinder 6 for filling powder into the valve pocket, and a main screw 5 is installed in the conveying cylinder 6, The main screw 5 is used to convey the powder forward, and the corresponding main screw 5 is equipped with a stopper worm gear 17. The stopper worm 17 cooperates with the main screw 5 in a corresponding spiral, so that the main screw 5 drives the stopper worm 17 to rotate, and the stopper worm 17 The worm gear teeth extend into the spiral groove of the main screw 5 to block the powder in the spiral groove, prevent the powder from rotating with the spiral groove, ensure that the main screw can effectively push the powder forward, and then build up the filling pressure.
[0049] In addition, since the inner diameter of the filling pipe 9 is smaller than the inner diameter of the conveyin...
specific Embodiment 2
[0070] Its difference with implementation: 1 mainly lies in: in embodiment 1, the agitating vane of boiling head is equal-pitch conical helical structure. In this embodiment, the structure of the boiling head is as Figure 8 As shown, the boiling head 10 also includes a base 101, the base 101 is used for fixed assembly with the front end of the inner drive shaft, and the stirring blade 102 is installed on the base 101, the stirring blade 102 is a spiral blade, and the spiral blade follows a logarithmic spiral The spiral blade extends along the circumferential direction of the boiling head gradually from the back to the front, and the outer diameter of the spiral blade gradually becomes smaller from the back to the front to correspond to the inner surface of the conical powder gathering cone.
[0071] There are two helical blades arranged symmetrically with respect to the central axis of the boiling head, and there is a gap at the side of the central axis of the boiling head co...
specific Embodiment 3
[0074] The main difference between it and Embodiment 2 is that in Embodiment 2, the center of the boiling head is hollow to form a hollow boiling head structure. In this embodiment, for the two-leaf helical blade, such as Figure 9 As shown, the boiling head 10 is provided with a central column 103 at the position of the central axis of the boiling head. The central column 103 extends along the front and rear directions. The central column 103 is a cone that gradually decreases from the back to the front. On the outer peripheral surface of the column 103, in this way, when a high-speed rotation is required, the central column 103 can effectively enhance the overall strength of the boiling head 10, and the tendency of rotation flutter is small.
[0075] In other embodiments, the central column can also be a cylindrical structure, which can also enhance the strength of the boiling head.
[0076] Here, the central column is arranged on the boiling head, so that the boiling head ...
PUM
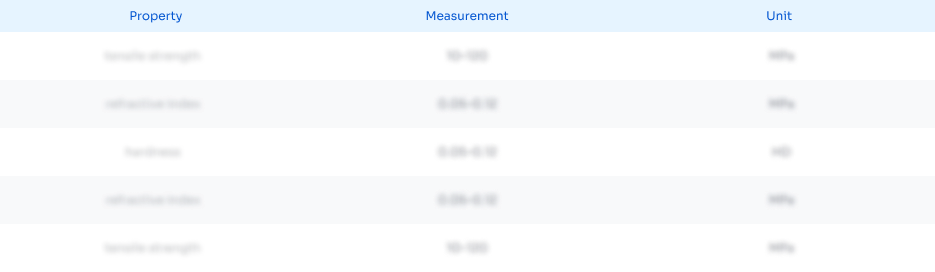
Abstract
Description
Claims
Application Information

- R&D Engineer
- R&D Manager
- IP Professional
- Industry Leading Data Capabilities
- Powerful AI technology
- Patent DNA Extraction
Browse by: Latest US Patents, China's latest patents, Technical Efficacy Thesaurus, Application Domain, Technology Topic, Popular Technical Reports.
© 2024 PatSnap. All rights reserved.Legal|Privacy policy|Modern Slavery Act Transparency Statement|Sitemap|About US| Contact US: help@patsnap.com