Split type flexible grasping robot for fragile objects and working method
A split-type technology for fragile items, applied in the direction of lifting devices, etc., can solve the problems of large handling of fragile items, irregular shape of fragile items that cannot be grasped and transported, and achieve the effect of efficient grasping
- Summary
- Abstract
- Description
- Claims
- Application Information
AI Technical Summary
Problems solved by technology
Method used
Image
Examples
Embodiment 1
[0086] Such as figure 1 As shown, a split-type flexible grabbing robot for fragile items includes a base 3, a split-type flexible grabbing module 1, and a lifting and moving module;
[0087] The bottom of the base 3 is provided with mobile wheels 3-10, which is convenient for the robot to move and carry the fragile items 2; specifically, as Figure 7 As shown, the base 3 includes a chassis body 3-8 in a U-shaped structure, and the inside of the two parallel sides of the chassis body 3-8 are respectively equipped with driving servo motors 3-9 for driving the moving wheels 3-10 at 4 corners. The top of the chassis body 3-8 is fixedly connected with the chassis end cover 3-7;
[0088] The lifting and moving module is located on the upper part of the base 3 and is fixedly connected with the base 3;
[0089] The split-type flexible grab module 1 is located on the top of the base 3 and is connected to the lifting and moving module, and the lifting and moving module controls the up...
Embodiment 2
[0108] Such as Figure 10 As shown, the item grabbing method based on the split type flexible grabbing robot of fragile items in embodiment 1 includes the following steps:
[0109] Step 11: The lifting servo motor 3-1 is started, so that the split-type flexible grabbing module 1 is lowered to the position where the fragile item 2 is to be grabbed; that is, the diamond-shaped gripping hole passes through the fragile item to be grabbed from top to bottom;
[0110] Step 12: The air compressor 4-1 pours high-pressure gas into the air tank 4-3 and reaches the preset pressure;
[0111] Step 13: The computer issues grabbing and handling instructions to the controller;
[0112] Step 14: The controllers in each pneumatic control unit set the limit pressures of the servo relief valves 4-6; usually, the set limit pressures of the servo relief valves 4-6 are the same;
[0113] Step 15: The controller in each pneumatic unit controls the coil P1 at the left end of the corresponding three-...
Embodiment 3
[0126] Such as Figure 11 As shown, the method for judging the shape of an item based on a split-type flexible grabbing robot for fragile items in Embodiment 1 includes the following steps:
[0127] Step 21: Start the lifting servo motor 3-1 to lower the split flexible grab module 1 to the position where the fragile item 2 is to be grabbed; that is, the diamond-shaped gripping hole passes through the fragile item to be grabbed from top to bottom;
[0128] Step 22: The air compressor 4-1 pours high-pressure gas into the air tank 4-3 and reaches the preset pressure;
[0129] Step 23: The computer issues a shape determination instruction to the controller;
[0130] Step 24: the controller in each pneumatic control unit sets the limit pressure of the servo overflow valve 4-6;
[0131] Step 25: The controller in each pneumatic control unit controls the coil P1 at the left end of the corresponding three-position four-way solenoid valve 4-5 to be energized, and the coil P2 at the r...
PUM
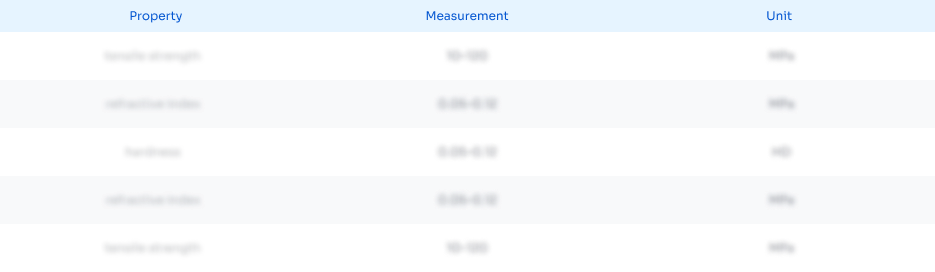
Abstract
Description
Claims
Application Information

- R&D
- Intellectual Property
- Life Sciences
- Materials
- Tech Scout
- Unparalleled Data Quality
- Higher Quality Content
- 60% Fewer Hallucinations
Browse by: Latest US Patents, China's latest patents, Technical Efficacy Thesaurus, Application Domain, Technology Topic, Popular Technical Reports.
© 2025 PatSnap. All rights reserved.Legal|Privacy policy|Modern Slavery Act Transparency Statement|Sitemap|About US| Contact US: help@patsnap.com