Preparation method of alkali lignin-based dye dispersant
A dye dispersant and alkali lignin technology, applied in the field of preparation of alkali lignin-based dye dispersants, can solve the problems of low dispersion grade, poor high temperature stability, strong fiber contamination, etc., and achieve high dispersion grade and high temperature stability. Good, low fiber contamination effect
- Summary
- Abstract
- Description
- Claims
- Application Information
AI Technical Summary
Problems solved by technology
Method used
Image
Examples
preparation example Construction
[0016] A preparation method of an alkali lignin-based dye dispersant, using alkali lignin in the pulp and paper industry as a raw material, comprising the following steps:
[0017] Using alkali lignin in the pulp and paper industry as raw material, purify alkali lignin by using organic solvent and acid precipitation method, and use a new alkylation system 1,6-dibromohexane / dimethylformamide to regulate alkali lignin molecules , to obtain molecularly regulated alkali lignin (CAL). Separation of medium and high molecular weight (3000-13000g / mol) alkali lignin (CAL) by ultrafiltration h ). at cal h CAL h :K 2 CO 3 =5:3 (w / w) Add potassium carbonate solid and place it in a three-necked flask, according to CAL h : DMF = 1: 5 (w: v) after mixing, put it in a water bath and heat it until it reaches 70-100 ° C, according to CAL h : 1,4-butane sultone=1:0.05~0.35 Add 1,4-butane sultone, and make the mixture sulfonate under stirring for 1~4h respectively. Pour the mixture into a...
Embodiment 1
[0032] Embodiment 1: The preparation of alkali lignin-based dye dispersant is realized through the following steps.
[0033] (1) Organic solvent purification of crude alkali lignin: add acidic dioxane aqueous solution (dioxane / water=9:1, v:v, pH=2). The mixture was stirred at 87°C for 2 hours, then centrifuged to remove the precipitate. The supernatant to which sodium bicarbonate was added was kept stirring for 3 hours to neutralize the acid in the solution. After centrifuging again to remove the precipitate, the supernatant was rotovapped under vacuum at 55 °C to remove and recover dioxane.
[0034] (2) Separation and purification of alkali lignin by acid precipitation: the supernatant after vacuum rotary evaporation was added to 2000 mL of hydrochloric acid solution (pH=2), and then centrifuged to obtain a precipitate. The precipitate was freeze-dried to obtain purified alkali lignin (PAL) as a solid powder.
[0035] (3) Alkylation of PAL: Dissolve PAL in dimethylformami...
Embodiment 2
[0042] Embodiment 2: The preparation of alkali lignin-based dye dispersant is realized through the following steps.
[0043] (1) Organic solvent purification of crude alkali lignin: add acidic dioxane aqueous solution (dioxane / water=9:1, v:v, pH=2). The mixture was stirred at 87°C for 2 hours, then centrifuged to remove the precipitate. The supernatant to which sodium bicarbonate was added was kept stirring for 3 hours to neutralize the acid in the solution. After centrifuging again to remove the precipitate, the supernatant was rotovapped under vacuum at 55 °C to remove and recover dioxane.
[0044] (2) Separation and purification of alkali lignin by acid precipitation: the supernatant after vacuum rotary evaporation was added to 2000 mL of hydrochloric acid solution (pH=2), and then centrifuged to obtain a precipitate. The precipitate was freeze-dried to obtain purified alkali lignin (PAL) as a solid powder.
[0045] (3) Alkylation of PAL: Dissolve PAL in dimethylformami...
PUM
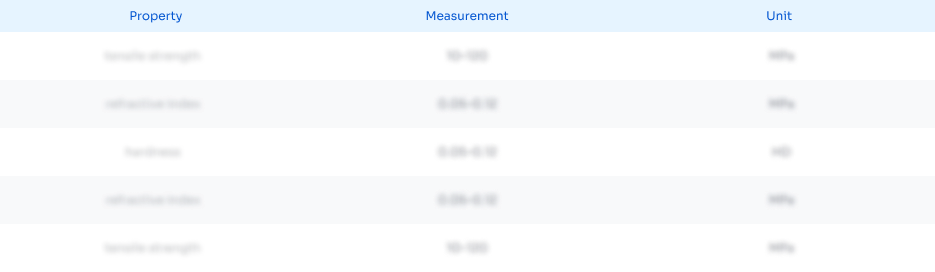
Abstract
Description
Claims
Application Information

- Generate Ideas
- Intellectual Property
- Life Sciences
- Materials
- Tech Scout
- Unparalleled Data Quality
- Higher Quality Content
- 60% Fewer Hallucinations
Browse by: Latest US Patents, China's latest patents, Technical Efficacy Thesaurus, Application Domain, Technology Topic, Popular Technical Reports.
© 2025 PatSnap. All rights reserved.Legal|Privacy policy|Modern Slavery Act Transparency Statement|Sitemap|About US| Contact US: help@patsnap.com