Automobile dynamic vibration absorption system and control method
A technology of dynamic vibration absorption and control method, which is applied in the direction of vibration suppression adjustment, non-rotational vibration suppression, shock absorber, etc., can solve the problems of small vibration damping frequency and range, narrow vibration damping frequency, etc., and achieve reduced amplitude and good The effect of comfort, mass and volume optimization
- Summary
- Abstract
- Description
- Claims
- Application Information
AI Technical Summary
Problems solved by technology
Method used
Image
Examples
Embodiment 1
[0074] Embodiment 1: For the automobile equipped with this vibration-absorbing system, the vibration-absorbing system of this embodiment is fixed on the A component of the automobile, the mass ratio of the selected vibration-absorbing unit and A-component is 0.1, and the natural frequency of the vibration-absorbing unit of this embodiment is determined is 120Hz, and the stiffness is 10000N / mm, according to the stiffness characteristic curve of the spring of the vibration-absorbing system of the present embodiment and Maxwell's electromagnetic force formula, the target current I of the first electromagnetic coil is calculated. 1 is 6.3A, according to the optimal damping ratio formula, the optimal damping ratio and viscous damping coefficient (respectively the optimal damping ratio and viscosity coefficient of the vibration-absorbing unit) can be obtained as 0.167 and 142.9N·S·m -1 , and then based on the characteristic curve of the damping coefficient of the magnetic fluid in th...
Embodiment 2
[0076] Embodiment 2: For the automobile equipped with this vibration-absorbing system, the vibration-absorbing system of this embodiment is fixed on the B component of the automobile, and the mass ratio of the selected vibration-absorbing unit to the B-component is 0.1, and the natural frequency of the vibration-absorbing unit of this embodiment is determined is 40Hz, and the stiffness is 500N / mm, according to the stiffness characteristic curve of the spring of the vibration-absorbing system of the present embodiment and Maxwell's electromagnetic force formula, the target current I of the first electromagnetic coil is calculated. 1 is 4A, according to the optimal damping ratio formula, the optimal damping ratio and viscous damping coefficient (respectively the optimal damping ratio and viscosity coefficient of the vibration-absorbing unit) can be obtained as 0.167 and 98.4N·S·m -1 , and then based on the characteristic curve of the damping coefficient of the magnetic fluid in t...
Embodiment 3
[0078] Embodiment 3: For the automobile equipped with this vibration-absorbing system, the vibration-absorbing system of this embodiment is fixed on the C component of the automobile, and the mass ratio of the selected vibration-absorbing unit to the C-component is 0.1, and the natural frequency of the vibration-absorbing unit of this embodiment is determined is 10Hz, stiffness is 100N / mm, according to the stiffness characteristic curve of the spring of the vibration-absorbing system of the present embodiment and Maxwell's electromagnetic force formula, calculate the target current I of the first electromagnetic coil 1 is 1.5A, according to the optimal damping ratio formula, the optimal damping ratio and viscous damping coefficient (respectively the optimal damping ratio and viscosity coefficient of the vibration-absorbing unit) can be obtained as 0.167 and 95.2N·S·m -1 , and then based on the characteristic curve of the damping coefficient of the magnetic fluid in the damping ...
PUM
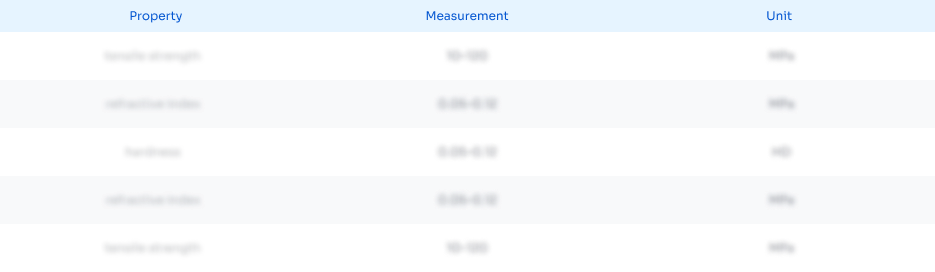
Abstract
Description
Claims
Application Information

- Generate Ideas
- Intellectual Property
- Life Sciences
- Materials
- Tech Scout
- Unparalleled Data Quality
- Higher Quality Content
- 60% Fewer Hallucinations
Browse by: Latest US Patents, China's latest patents, Technical Efficacy Thesaurus, Application Domain, Technology Topic, Popular Technical Reports.
© 2025 PatSnap. All rights reserved.Legal|Privacy policy|Modern Slavery Act Transparency Statement|Sitemap|About US| Contact US: help@patsnap.com