Combined tool with cooling function for machining stepped holes
A technology of combining cutting tools and cooling holes, which is applied in the direction of step drilling, manufacturing tools, metal processing equipment, etc., can solve the problems of large investment in equipment and cutting tools, low production efficiency, long working hours, etc., and achieve good cooling effect.
- Summary
- Abstract
- Description
- Claims
- Application Information
AI Technical Summary
Problems solved by technology
Method used
Image
Examples
Embodiment Construction
[0018] The following will clearly and completely describe the technical solutions in the embodiments of the present invention with reference to the accompanying drawings in the embodiments of the present invention. Obviously, the described embodiments are only some, not all, embodiments of the present invention.
[0019] Refer to attached Figure 1~3 , according to the number of cutting edges and edge grooves of the milling cutter (1), select the adjusting bushing (2) of different height and diameter, and screw the thread on the threaded straight shank (3-2) of the twist drill (3) into the milling cutter In the thread (1-6) of the cutter (1) until it is fastened, when working, the coolant flows through the cooling hole (1-1) of the milling cutter (1) to the relief groove (1-5), and through the twist drill The two cooling holes (3-1) on (3) flow out of the cooling hole, and the chips are discharged through the edge groove of the twist drill (3) and the edge groove of the millin...
PUM
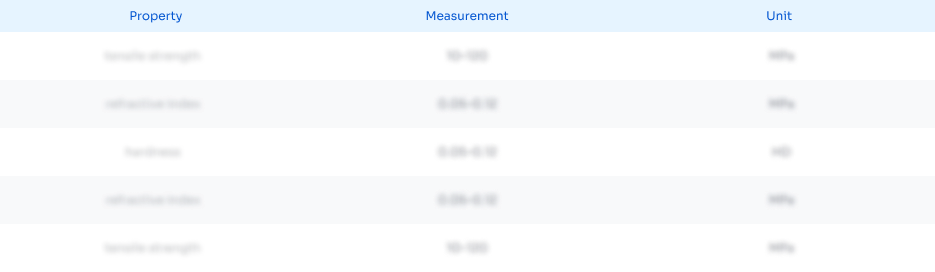
Abstract
Description
Claims
Application Information

- R&D
- Intellectual Property
- Life Sciences
- Materials
- Tech Scout
- Unparalleled Data Quality
- Higher Quality Content
- 60% Fewer Hallucinations
Browse by: Latest US Patents, China's latest patents, Technical Efficacy Thesaurus, Application Domain, Technology Topic, Popular Technical Reports.
© 2025 PatSnap. All rights reserved.Legal|Privacy policy|Modern Slavery Act Transparency Statement|Sitemap|About US| Contact US: help@patsnap.com