Dynamic modeling method and system for mine multi-rope winding type elevator and storage medium
A technology of mechanical modeling and dynamic model, applied in the direction of instrumentation, design optimization/simulation, electrical digital data processing, etc., can solve problems such as low lateral stiffness and deepen the difficulty of dynamic analysis of hoist system, and achieve the goal of modeling method simple effect
- Summary
- Abstract
- Description
- Claims
- Application Information
AI Technical Summary
Problems solved by technology
Method used
Image
Examples
Embodiment 1
[0078] The high-fidelity dynamic modeling method of multi-rope winding flexible tank hoist based on three-dimensional space provided by this embodiment includes the following steps:
[0079] The entire system is decomposed into several subsystems from the level of physical components, generally including three systems: hoisting rope, cage, and tank road. Wherein the hoisting rope system includes three parts: hanging rope, sky wheel and hanging rope.
[0080] Each subsystem is modeled with zero boundary conditions, as follows:
[0081] Model the hoisting rope system, describe the dynamic characteristics of the rope in the absolute coordinate system, consider the three-dimensional vibration of the hoisting rope, and write the kinetic energy and potential energy of the hoisting rope system. Write the energy dissipation of the hoist rope system according to the viscous damping model. Finally, using Hamilton's principle, the dynamic equation of the subsystem is obtained under the...
Embodiment 2
[0091] Such as figure 1 as shown, figure 1 It is a schematic diagram of a typical multi-rope winding ultra-deep flexible tank elevator. It is assumed that the rotation of the drum is well controlled, that is, the rotation of the drum is completely consistent with the target lifting curve, and the dynamic response of the drum is ignored in this model. Only the boundary conditions caused by the rollers are introduced in this method. The rope between the drum and the sky wheel is called a suspension rope, and the rope between the sky wheel and the cage is called a suspension rope. At the initial moment, that is, when the lifting has not been carried out, a fixed coordinate system O is established at the midpoint of the line connecting the tangent points between the two drums and the suspension rope c x c the y c z c , establish a fixed coordinate system O at the midpoint of the line connecting the two vertical ropes with the tangent point v x v the y v z v . The length ...
PUM
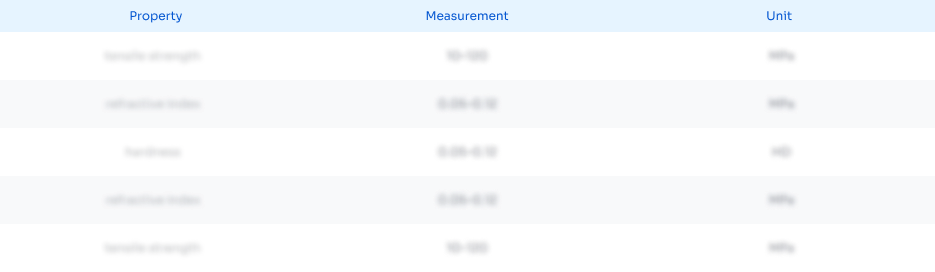
Abstract
Description
Claims
Application Information

- R&D
- Intellectual Property
- Life Sciences
- Materials
- Tech Scout
- Unparalleled Data Quality
- Higher Quality Content
- 60% Fewer Hallucinations
Browse by: Latest US Patents, China's latest patents, Technical Efficacy Thesaurus, Application Domain, Technology Topic, Popular Technical Reports.
© 2025 PatSnap. All rights reserved.Legal|Privacy policy|Modern Slavery Act Transparency Statement|Sitemap|About US| Contact US: help@patsnap.com