Full-automatic high-sensitivity pipe network leakage monitoring sensor
A technology for monitoring sensors and sensitive tubes, which is applied in the field of sensors, can solve problems such as complex structures, and achieve the effects of low cost, good precision and reliability
- Summary
- Abstract
- Description
- Claims
- Application Information
AI Technical Summary
Problems solved by technology
Method used
Image
Examples
Embodiment 1
[0032] A kind of fully automatic high-sensitivity pipe network leakage monitoring sensor of the present invention, such as figure 1 As shown, it includes a check valve body 1 and a sensor body 2. A medium channel 3 is provided inside the check valve body 1. The two ends of the medium channel 3 are respectively a medium inlet and a medium outlet 32. The center position of the medium inlet and the medium outlet 32 is A first valve seat 33 and a second valve seat 34 coaxially arranged with the check valve body 1 are provided respectively, and a valve core 4 is interspersed on the first valve seat 33 and the second valve seat 34, and a valve core 4 is sleeved on the valve core 4. A spring 6 is installed between the valve core 4 and the second valve seat 34. The valve core 4 is guided by the first valve seat 33 and the second valve seat 34. Under the action of the spring 6, the valve disc 5 is driven to move and close the medium inlet. The check valve body 1 is installed on the p...
Embodiment 2
[0045] refer to figure 2 , in order to better sample the flow field, add a probe on the basis of implementation one, the newly added probe is the second probe 22, and the newly added second probe 22 is set at the position between the first probe 21 and the pipe wall superior.
[0046]The flow velocity signals of the two probes are collected separately, and then comprehensively calculate and output the flow digital value, providing two sampling values of the internal flow field (radial curve) of the pipeline 7, and the flow rate can be calculated by fitting the flow field curve. The flow rate can be obtained through real-time table lookup; the lookup table is obtained in advance through fitting calculation or actual flow test.
Embodiment 3
[0048] refer to image 3 , the sensor body 2 also has a single-chip microcomputer, which executes as image 3 Data processing steps shown. Proceed as follows:
[0049] S201: Sampling, sampling the flow velocity signal of the probe 21, the sampling accuracy is 12 bits, and the sampling frequency is 100 Hz;
[0050] S202: judge laminar flow / turbulent flow, that is, calculate the noise level for the original signal, and judge laminar flow / turbulent flow accordingly;
[0051] S203: calculate flow rate;
[0052] S204: outputting, that is, providing the flow data to an external device.
[0053] The above steps are executed cyclically.
[0054] Under water spraying conditions, the fire hose is always in a turbulent state (Reynolds number is much greater than 2300), but usually because the absolute value of the leakage flow is very small, even if a high flow rate is formed on the probe, it is still a laminar flow. The step S202 of judging laminar / turbulent flow S202 is based on ...
PUM
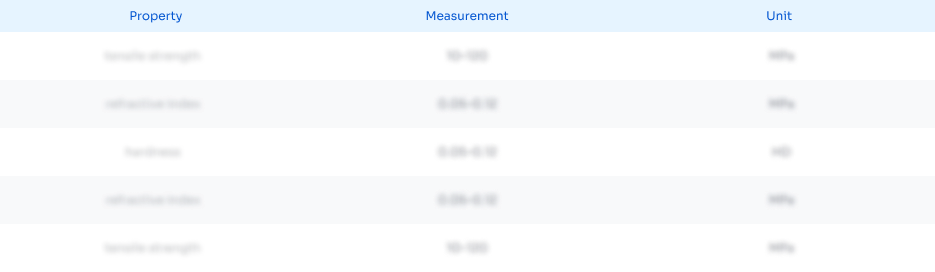
Abstract
Description
Claims
Application Information

- Generate Ideas
- Intellectual Property
- Life Sciences
- Materials
- Tech Scout
- Unparalleled Data Quality
- Higher Quality Content
- 60% Fewer Hallucinations
Browse by: Latest US Patents, China's latest patents, Technical Efficacy Thesaurus, Application Domain, Technology Topic, Popular Technical Reports.
© 2025 PatSnap. All rights reserved.Legal|Privacy policy|Modern Slavery Act Transparency Statement|Sitemap|About US| Contact US: help@patsnap.com