Bulk packing machine with material level detection structure for charging and method thereof
A material level detection, bulk machine technology, applied in the directions of transportation and packaging, loading/unloading, etc., can solve the problems of regulation that cannot be loaded into the bulk machine, easy to be pressed under the material, poor protection effect, etc., to improve the use of Flexibility, easy dust protection effect
- Summary
- Abstract
- Description
- Claims
- Application Information
AI Technical Summary
Problems solved by technology
Method used
Image
Examples
Embodiment approach
[0047] Another technical solution proposed by the present invention: providing a method for implementing a bulk packing machine with a material level detection structure for charging, comprising the following steps:
[0048] Step 1: Insert the telescopic tube 13 into the container to be loaded as a whole, and make the bottom of the detection rod 123 contact with the bottom of the telescopic tube 13;
[0049] Step 2: Start loading materials into the device to be loaded. With the increase of materials, the telescopic tube 13 gradually moves upwards under the control of the servo motor 15. At this time, the ferrule 193 is moved upwards, and the gap between the sensor 194 and the receiver 124 According to the cooperation between them, the material level of the material inside the loader can be obtained by calculating h=5i+20 through the formula, and it will be displayed in real time on the main controller 14;
[0050] Step 3: During the material conveying process, the extension pi...
PUM
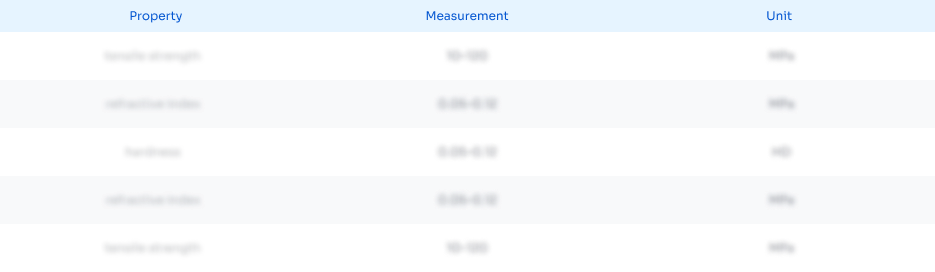
Abstract
Description
Claims
Application Information

- R&D
- Intellectual Property
- Life Sciences
- Materials
- Tech Scout
- Unparalleled Data Quality
- Higher Quality Content
- 60% Fewer Hallucinations
Browse by: Latest US Patents, China's latest patents, Technical Efficacy Thesaurus, Application Domain, Technology Topic, Popular Technical Reports.
© 2025 PatSnap. All rights reserved.Legal|Privacy policy|Modern Slavery Act Transparency Statement|Sitemap|About US| Contact US: help@patsnap.com