Spatial orientation measuring instrument precision evaluation method based on single-star projection
A technology of measuring instruments and space pointing, applied in the direction of instruments, measuring devices, etc., can solve problems such as difficult to accurately evaluate precision indicators, difficult to evaluate extremely high-precision indicators, etc., and achieve scientific evaluation results
- Summary
- Abstract
- Description
- Claims
- Application Information
AI Technical Summary
Problems solved by technology
Method used
Image
Examples
Embodiment Construction
[0041] Specific embodiments of the present invention will be further described in detail below in conjunction with the accompanying drawings.
[0042] figure 1 It is an imaging model of the space extremely high-precision measuring instrument of the present invention. The surveying instrument obtains the spacecraft's three-axis inertial attitude and target pointing information by taking a star map and performing steps such as star point extraction, matching recognition, and attitude determination. The accuracy evaluation described in the method of the invention can be carried out on the track in real time, and can also be carried out by using the telemetry data package transmitted on the track.
[0043] like figure 2 As shown, the present invention proposes a method for evaluating the on-orbit accuracy of a space extremely high-precision pointing and measuring instrument, and the steps are as follows:
[0044] (1) During the on-orbit working process of the surveying instrum...
PUM
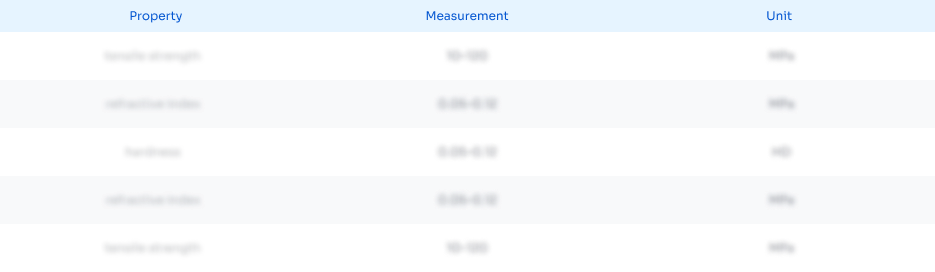
Abstract
Description
Claims
Application Information

- Generate Ideas
- Intellectual Property
- Life Sciences
- Materials
- Tech Scout
- Unparalleled Data Quality
- Higher Quality Content
- 60% Fewer Hallucinations
Browse by: Latest US Patents, China's latest patents, Technical Efficacy Thesaurus, Application Domain, Technology Topic, Popular Technical Reports.
© 2025 PatSnap. All rights reserved.Legal|Privacy policy|Modern Slavery Act Transparency Statement|Sitemap|About US| Contact US: help@patsnap.com