Preparation method of molybdenum oxide catalyst with hydrotalcite-like structure and application thereof in synthesis of methacrylic acid from isobutyraldehyde
A hydrotalcite structure, catalyst technology, applied in the direction of metal/metal oxide/metal hydroxide catalyst, organic compound preparation, physical/chemical process catalyst, etc. The effect of rich specific surface area and high selectivity
- Summary
- Abstract
- Description
- Claims
- Application Information
AI Technical Summary
Problems solved by technology
Method used
Image
Examples
Embodiment 1
[0026] Prepare the ammonium molybdate solution with a concentration of 0.2mol / L, the zinc nitrate solution with a concentration of 2mol / L, and the aluminum nitrate solution with a concentration of 2mol / L, mix and stir in equal volumes, and the stirring rate is 500r / min, and then the excess concentration is 1mol / L sodium carbonate solution (the addition of sodium carbonate is 1.5 times the total molar weight of ammonium molybdate, zinc nitrate and aluminum nitrate), using a liquid phase pump to slowly drop into the mixed solution at a flow rate of 1mL / min, continue to stir after dropping 5h, then aged for 6h, filtered after aging, washed the solid, and dried in an oven at 120°C to obtain the precursor.
[0027] Put the prepared precursor into a muffle furnace, the heating rate of the muffle furnace is 5°C / min, the calcination temperature is 450°C, and the calcination time is 5h, to obtain Mo 2 o 3 / Al 2 o 3 @ZnO Catalyst.
[0028] React the prepared catalyst in a fixed-bed...
Embodiment 2
[0034] Prepare the ammonium molybdate solution with a concentration of 1mol / L, the zinc nitrate solution with a concentration of 1.5mol / L, and the aluminum nitrate solution with a concentration of 3mol / L, mix and stir in equal volumes, and the stirring rate is 500r / min, and then make the excess concentration 1mol / L / L sodium carbonate solution (the addition of sodium carbonate is 1.4 times the total molar weight of ammonium molybdate, zinc nitrate and aluminum nitrate), using a liquid phase pump to slowly drop into the mixed solution at a flow rate of 3mL / min, continue stirring after dropping 4h, then aged for 10h, filtered after aging, washed the solid, and dried in an oven at 120°C to obtain the precursor.
[0035] Put the prepared precursor into a muffle furnace, the heating rate of the muffle furnace is 3°C / min, the calcination temperature is 600°C, and the calcination time is 3h, to obtain Mo 2 o 3 / Al 2 o 3@ZnO Catalyst.
[0036] React the prepared catalyst in a fixe...
Embodiment 3
[0038] Prepare the ammonium molybdate solution with a concentration of 0.5mol / L, the zinc nitrate solution with a concentration of 2mol / L, and the aluminum nitrate solution with a concentration of 2mol / L, mix and stir in equal volumes, and the stirring rate is 500r / min, and then the excess concentration is 1mol / L sodium carbonate solution (the molar addition of sodium carbonate is 1.4 times the total molar weight of ammonium molybdate, zinc nitrate and aluminum nitrate), using a liquid phase pump to slowly drip into the mixed solution at a flow rate of 2mL / min, continue to Stir for 3 hours, then age for 7 hours, filter after aging, wash the solid, and dry it in an oven at 120°C to obtain a precursor.
[0039] Put the prepared precursor into a muffle furnace, the heating rate of the muffle furnace is 3°C / min, the calcination temperature is 550°C, and the calcination time is 4h, to obtain Mo 2 o 3 / Al 2 o 3 @ZnO Catalyst.
[0040] React the prepared catalyst in a fixed-bed ...
PUM
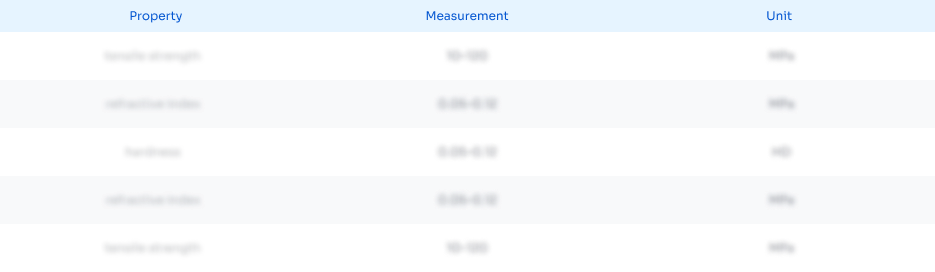
Abstract
Description
Claims
Application Information

- Generate Ideas
- Intellectual Property
- Life Sciences
- Materials
- Tech Scout
- Unparalleled Data Quality
- Higher Quality Content
- 60% Fewer Hallucinations
Browse by: Latest US Patents, China's latest patents, Technical Efficacy Thesaurus, Application Domain, Technology Topic, Popular Technical Reports.
© 2025 PatSnap. All rights reserved.Legal|Privacy policy|Modern Slavery Act Transparency Statement|Sitemap|About US| Contact US: help@patsnap.com