A MEMS Accelerometer Temperature Drift Error Estimation Method Based on Silicon Microstructure Analysis
An accelerometer and structural analysis technology, applied in the direction of speed/acceleration/shock measurement, speed/acceleration/shock measurement equipment testing/calibration, neural learning methods, etc., can solve the temperature drift error temperature of the MEMS accelerometer that has not been fully explored Relevant quantities, inaccurate modeling of estimated temperature drift errors, inaccurate estimation of MEMS accelerometer temperature drift errors, etc., achieve real-time estimation, improved environmental adaptability, and simple structure
- Summary
- Abstract
- Description
- Claims
- Application Information
AI Technical Summary
Problems solved by technology
Method used
Image
Examples
specific Embodiment approach 1
[0028] DETAILED DESCRIPTION OF THE PREFERRED EMBODIMENT One, a MEMS accelerometer temperature drift error estimation method based on silicon microstructure analysis described in the present embodiment, the method specifically includes the following steps:
[0029] Step 1. Obtain the temperature-related quantity used to estimate the temperature drift error of the MEMS accelerometer
[0030] Since the sensing circuit of the MEMS accelerometer has a comb structure, the sensing circuit of the MEMS accelerometer can be abstracted as a plate capacitor composed of a moving plate and a fixed plate. Due to the temperature dependence of the silicon-based material, when the ambient temperature When changing, the comb tooth structure undergoes structural deformation, and causes the internal structure of the MEMS accelerometer to present a three-dimensional space change, based on the plate capacitance calculation formula Deduce the capacitance output deviation before and after the ambient...
specific Embodiment approach 2
[0036] Specific implementation mode two: the difference between this implementation mode and specific implementation mode one is that the specific process of the step one is:
[0037] When the ambient temperature is T 0 , the overlapping length of the moving plate and the fixed plate is b 0 , the thickness of the comb teeth of the moving plate and the comb teeth of the fixed plate are both j 0 , the distance between the comb teeth of the moving plate and the comb teeth of the fixed plate is u0 , after simplification, the output capacitance value ΔC at this time 0 for:
[0038]
[0039] Among them, ε 0 is the dielectric constant;
[0040] When the ambient temperature change is T, it is assumed that the acceleration of the carrier to be detected and the ambient temperature are T 0 When the acceleration of the carrier to be detected is the same, the change of the ambient temperature is ΔT=T-T 0 , due to the temperature dependence of silicon-based materials, the internal ...
specific Embodiment approach 3
[0055] Specific embodiment three: the difference between this embodiment and specific embodiment one or two is that the BP neural network uses the crtbp function to complete the initialization of weights and bias parameters, and uses the GA (genetic) algorithm to initialize the weights and biases. Set parameters for selection, crossover and mutation, and then use the bs2rv function to decode the data after selection, crossover and mutation, and use the decoded data as the initial particle parameters of the PSO (particle swarm optimization) algorithm;
[0056] After decoding the output of the PSO algorithm, the decoding result is used as the initial weight and bias of the BP neural network.
[0057] The fitness fitness function is used to obtain the mean square error based on the measured data, initial weight and bias as the particle fitness, and guide the PSO algorithm to update the speed and position.
[0058] Take advantage of the velocity update operator v k+1 =v k +c 1 ...
PUM
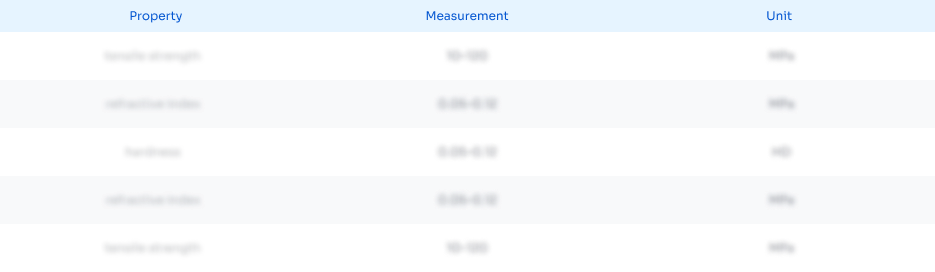
Abstract
Description
Claims
Application Information

- R&D Engineer
- R&D Manager
- IP Professional
- Industry Leading Data Capabilities
- Powerful AI technology
- Patent DNA Extraction
Browse by: Latest US Patents, China's latest patents, Technical Efficacy Thesaurus, Application Domain, Technology Topic, Popular Technical Reports.
© 2024 PatSnap. All rights reserved.Legal|Privacy policy|Modern Slavery Act Transparency Statement|Sitemap|About US| Contact US: help@patsnap.com