Preparation process of antistatic knitted fabric
A technology for knitted fabric and preparation process, which is applied in the processing of textile materials, continuous processing of textile materials, knitting and other directions, can solve the problems of complex preparation process and low product performance, and achieves simple preparation process operation, soft hand feeling and comfort. Good results
- Summary
- Abstract
- Description
- Claims
- Application Information
AI Technical Summary
Problems solved by technology
Method used
Examples
Embodiment 1
[0019] The present invention provides the following technical solutions: a preparation process of antistatic knitted fabric, the preparation process includes the following steps:
[0020] A. Firstly, prepare the knitted fabric raw materials;
[0021] B. Feed the knitted fabric raw materials into the knitting machine and knit to obtain the semi-finished fabric;
[0022] C. Add the semi-finished fabric to the high-temperature steam machine for high-temperature steam treatment;
[0023] D. Dyeing the fabric after high temperature steam treatment;
[0024] E. Finally, dry and shape the dyed fabric.
[0025] In this embodiment, the knitted fabric raw material in step A is composed of 20% silk fiber, 20% gabardine fiber, 10% flax fiber, 25% mohair fiber, and 25% imported long cotton fiber.
[0026] In the present embodiment, the tension of feeding silk fiber, gabardine fiber, and flax fiber in step B is 3g; the tension of feeding of described mohair fiber and imported long cotton...
Embodiment 2
[0032] A preparation process for an antistatic knitted fabric, the preparation process comprising the following steps:
[0033] A. First prepare the knitted fabric raw materials;
[0034] B. Feed the knitted fabric raw materials into the knitting machine and knit to obtain the semi-finished fabric;
[0035] C. Add the semi-finished fabric to the high-temperature steam machine for high-temperature steam treatment;
[0036] D. Dyeing the fabric after high temperature steam treatment;
[0037] E. Finally, dry and shape the dyed fabric.
[0038] In this embodiment, the knitted fabric raw material in step A is composed of 20% silk fiber, 20% gabardine fiber, 10% flax fiber, 25% mohair fiber, and 25% imported long cotton fiber.
[0039] In the present embodiment, the tension of silk fiber, gabardine fiber, and linen fiber feeding in step B is 5g; the tension of described mohair fiber and imported long cotton linter fiber feeding is 6g.
[0040] In this embodiment, the temperatur...
Embodiment 3
[0045] A preparation process for an antistatic knitted fabric, the preparation process comprising the following steps:
[0046] A. First prepare the knitted fabric raw materials;
[0047] B. Feed the knitted fabric raw materials into the knitting machine and knit to obtain the semi-finished fabric;
[0048] C. Add the semi-finished fabric to the high-temperature steam machine for high-temperature steam treatment;
[0049] D. Dyeing the fabric after high temperature steam treatment;
[0050] E. Finally, dry and shape the dyed fabric.
[0051] In this embodiment, the knitted fabric raw material in step A is composed of 20% silk fiber, 20% gabardine fiber, 10% flax fiber, 25% mohair fiber, and 25% imported long cotton fiber.
[0052] In the present embodiment, the tension of feeding silk fiber, gabardine fiber, and flax fiber in step B is 3g; the tension of feeding of described mohair fiber and imported long cotton linter fiber is 6g.
[0053] In this embodiment, the temperat...
PUM
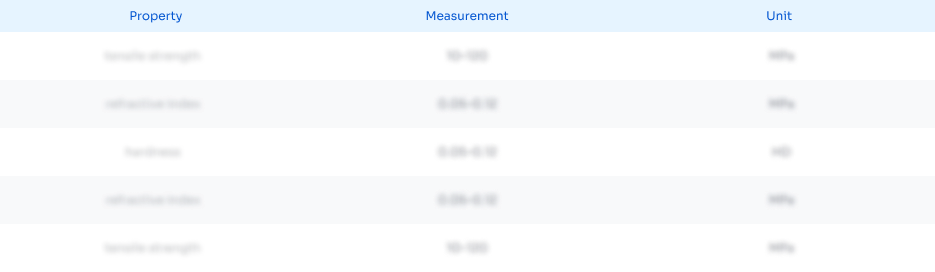
Abstract
Description
Claims
Application Information

- Generate Ideas
- Intellectual Property
- Life Sciences
- Materials
- Tech Scout
- Unparalleled Data Quality
- Higher Quality Content
- 60% Fewer Hallucinations
Browse by: Latest US Patents, China's latest patents, Technical Efficacy Thesaurus, Application Domain, Technology Topic, Popular Technical Reports.
© 2025 PatSnap. All rights reserved.Legal|Privacy policy|Modern Slavery Act Transparency Statement|Sitemap|About US| Contact US: help@patsnap.com