Chemical fabric cover plate type flame-retardant layer coating process
A coating process and cloth cover technology, used in textiles and papermaking, etc., can solve the problems of degumming of the cloth surface and insufficient bonding of the cloth surface.
- Summary
- Abstract
- Description
- Claims
- Application Information
AI Technical Summary
Problems solved by technology
Method used
Image
Examples
Embodiment 1
[0044] see figure 1 , a chemical fiber cloth cover sheet flame retardant layer coating process, comprising the following steps:
[0045] S1. Lay the chemical fiber cloth flat for tentering, clean the surface, and prepare flame retardant glue for later use;
[0046] S2. Arranging the stretched chemical fibers under a plurality of permeation-promoting cover sheets 2, connecting the permeation-promoting cover sheets 2 to the fixed surface through multiple elastic pull cords 1, and spraying flame-retardant glue on the surface of the chemical fiber cloth;
[0047] S3. Apply a magnetic field under the chemical fiber cloth to attract the permeation-promoting cover sheet 2 to move down to cover the chemical fiber cloth to promote the penetration of the flame retardant glue;
[0048] S4. Cancel the magnetic field and reapply the magnetic field after the permeation aid cover sheet 2 is reset, and the angle gradually changes until the surface of the chemical fiber cloth is covered;
[...
PUM
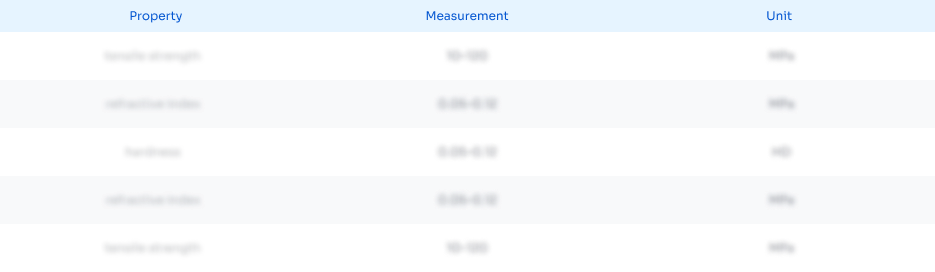
Abstract
Description
Claims
Application Information

- R&D
- Intellectual Property
- Life Sciences
- Materials
- Tech Scout
- Unparalleled Data Quality
- Higher Quality Content
- 60% Fewer Hallucinations
Browse by: Latest US Patents, China's latest patents, Technical Efficacy Thesaurus, Application Domain, Technology Topic, Popular Technical Reports.
© 2025 PatSnap. All rights reserved.Legal|Privacy policy|Modern Slavery Act Transparency Statement|Sitemap|About US| Contact US: help@patsnap.com