Rectangular concrete column-H-shaped beam composite ring plate type connecting joint and connecting method
A technology for concrete columns and connecting nodes, which can be used in buildings, building structures, etc., and can solve the problems of small size, large welding workload, and high welding process requirements.
- Summary
- Abstract
- Description
- Claims
- Application Information
AI Technical Summary
Problems solved by technology
Method used
Image
Examples
Embodiment 1
[0047] see figure 1 and figure 2 , the rectangular concrete column-H-shaped beam composite ring plate connection node in this embodiment, which includes a ring plate 3, at the junction of the upper flange plate of the H-shaped steel beam 4 and the rectangular concrete-filled steel tube column 1 and at the junction of the H-shaped steel beam 4 The connection between the lower flange plate and the rectangular concrete-filled steel tube column 1 is provided with an annular connecting plate 5, which is sleeved on the rectangular concrete-filled steel tube column 1 and welded to the rectangular concrete-filled steel tube column 1. A ring plate 3 is provided above the annular connecting plate 5 and below the annular connecting plate 5 of the upper flange plate, and a ring plate 3 is provided above the annular connecting plate 5 of the lower flange plate and below the annular connecting plate 5 of the lower flange plate , the ring plate 3 is sleeved around the rectangular steel tub...
Embodiment 2
[0049] The difference from Example 1 is that in this example, the rectangular concrete column-H-shaped beam composite ring plate connection node, its t 1 The value of is 21㎜, the width of the H-shaped steel beam 4 is 300㎜, b 1 =0.7*300㎜=210㎜, t 2 = t 3 = 25㎜, b 2 =b 3 =60㎜, then (b 1 *t 1 ) / (b2 *t 2 ) = (b 1 *t 1 ) / (b 3 *t 3 )=(210*21) / (60*25)=2.94, rounded m=n=3, that is, the number of ring plates 3 at the corresponding position of the upper flange plate is 6, and the ring plate at the corresponding position of the lower flange plate The number of 3 is 6, then the thickness t of the upper flange plate 4 ≥23㎜, the thickness of the lower flange plate t 5 ≥23㎜; the distance between two adjacent ring plates 3 above the annular connecting plate 5 of the upper flange plate and below the annular connecting plate 5 of the upper flange plate is 50 mm, and at the annular connecting plate 5 of the lower flange plate The distance between two adjacent ring plates 3 below the ...
Embodiment 3
[0051] The difference from Example 1 is that in this example, the rectangular concrete column-H-beam composite ring plate connection node has 10 ring plates 3 at the corresponding position of the upper flange plate, and 10 ring plates 3 at the corresponding position of the lower flange plate. The number of 3 is 10, and the distance between two adjacent ring plates 3 above the annular connecting plate 5 of the upper flange plate and below the annular connecting plate 5 of the upper flange plate is 80mm, and at the annular connecting plate 5 of the lower flange plate The distance between two adjacent ring plates 3 above the connecting plate 5 and below the annular connecting plate 5 of the upper flange plate is 80mm; the rest are the same as in the first embodiment.
PUM
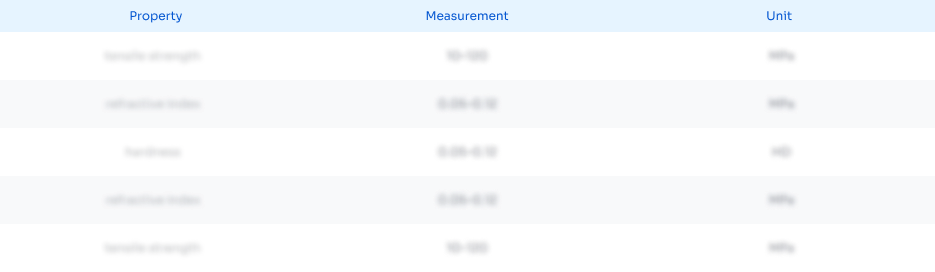
Abstract
Description
Claims
Application Information

- Generate Ideas
- Intellectual Property
- Life Sciences
- Materials
- Tech Scout
- Unparalleled Data Quality
- Higher Quality Content
- 60% Fewer Hallucinations
Browse by: Latest US Patents, China's latest patents, Technical Efficacy Thesaurus, Application Domain, Technology Topic, Popular Technical Reports.
© 2025 PatSnap. All rights reserved.Legal|Privacy policy|Modern Slavery Act Transparency Statement|Sitemap|About US| Contact US: help@patsnap.com