Production process of environment-friendly degradable plastic film
A technology of plastic film and production process, which is applied in the field of production process of environmentally friendly and degradable plastic film, and can solve the problems of inability, degradation, and production process that cannot guarantee production efficiency, etc.
- Summary
- Abstract
- Description
- Claims
- Application Information
AI Technical Summary
Problems solved by technology
Method used
Examples
Embodiment 1
[0037] First, 65 parts of the raw material polyethylene plastic particles, 37 polylactic plastic particles, 9 starch plastic particles, 3.4 parts of maleic anhydride, 2.6 defoamides, and 1.5 parts of dikyl phthalate. At the same time, the polyethylene plastic particles, polylactic acid plastic particles and starch plastic particles are screened to 80 mesh;
[0038] The polyethylene plastic particles, polylactic acid plastic particles, and starch plastic particles are melted at a temperature of from 190 ° C, and the stirring is mixed, and the maleic anhydride graft compatible agent, defoamer, and octyl phthalate are added to 155 ° C. Stir mixing;
[0039] The feedstock mixed in the above-described T-type die casting was extruded, and the extruded film was cooled by a cooling roller of 1 ° C, and then the film was milled by a flattening device. Film creates wrinkles;
[0040] The film was rinsed by uniformly disposed uniformly provided by the film on both sides, and after the 1.2m h...
Embodiment 2
[0043] First, 75 parts of the raw material polyethylene plastic particles, 39 polylactic acid plastic particles, 8 starch plastic particles, 3.8 maleic anhydride graft compatible agents, 1.8 defoamodulators, and 1.8 dikyl phthalate. At the same time, the polyethylene plastic particles, polylactic acid plastic particles and starch plastic particles are sieved to 120 mesh;
[0044] The polyethylene plastic particles, polylactic acid plastic particles, and the starch plastic particles are melted under 200 ° C at the temperature conditions, and the mixture is added to 155 ° C to add maleic anhydride graft compatibilizer, defoamer, and dictyl phthalate. Stir mixing;
[0045] The feedstock mixed in the above-described T-type die casting was extruded, and the extruded film was subjected to a cooling roll of -1 ° C to cool the film, and then the film was milled by a flattening device. Avoid the formation of pleats;
[0046]The film was rinsed by uniformly disposed uniformly disposed of th...
Embodiment 3
[0049] First, 58 raw material polyethylene plastic particles, 41 polylactic plastic particles, 10 starch plastic particles, 2.3 parts of maleic anhydride graft compatible agent, 3.2 parts of defoamide, and octyl phthalate 1.8 parts. At the same time, the polyethylene plastic particles, polylactic acid plastic particles and starch plastic particles are sieved to 100 mesh;
[0050] The polyethylene plastic particles, polylactic acid plastic particles, and starch plastics are simultaneously stirred at a temperature of 180 ° C, and then add a maleic anhydride graft compatible agent, anhydrutant, and dictyl phthalate. Stir mixing;
[0051] The feedstock mixed in the above-described T-type die casting was extruded, and the extruded film was cooled by a cooling roller of 1 ° C, and then the film was milled by a flattening device. Film creates wrinkles;
[0052] The film was rinsed by uniformly disposed uniformly provided by the film on the upper and lower sides, and then dried after the ...
PUM
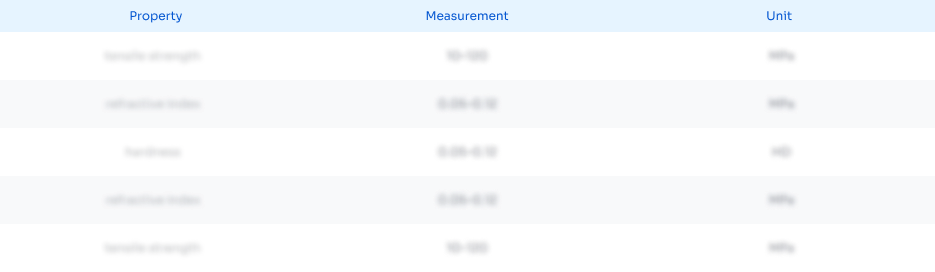
Abstract
Description
Claims
Application Information

- R&D Engineer
- R&D Manager
- IP Professional
- Industry Leading Data Capabilities
- Powerful AI technology
- Patent DNA Extraction
Browse by: Latest US Patents, China's latest patents, Technical Efficacy Thesaurus, Application Domain, Technology Topic, Popular Technical Reports.
© 2024 PatSnap. All rights reserved.Legal|Privacy policy|Modern Slavery Act Transparency Statement|Sitemap|About US| Contact US: help@patsnap.com