Multi-body collaborative omnidirectional transfer intelligent robot traction system and method
An intelligent robot and traction system technology, applied in aircraft parts, transportation and packaging, ground installations, etc., can solve the problems of high work intensity of personnel, low efficiency of manual traction operation, and hidden safety hazards.
- Summary
- Abstract
- Description
- Claims
- Application Information
AI Technical Summary
Problems solved by technology
Method used
Image
Examples
Embodiment Construction
[0049] Attached below Figure 2-14 Taking examples together, the traction system of the multi-body cooperative omnidirectional transfer intelligent robot of the present invention will be described in detail.
[0050] Such as figure 2 , the multi-body collaborative omnidirectional transfer intelligent robot traction system of the present invention is presented by three light-duty omnidirectional intelligent transfer vehicles (including 1 front vehicle 1 and 2 rear vehicles (the first rear vehicle 2 and the second rear vehicle 3) The font layout is combined, the front car 1 is docked with the aircraft front landing gear wheel, and the rear car (the first rear car 2 and the second rear car 3) is docked with the main landing gear wheel.
[0051] The structure of the light omnidirectional intelligent transfer vehicle in the multi-body cooperative omnidirectional transfer intelligent robot traction system is basically the same, including the car body or chassis module 6, the omnid...
PUM
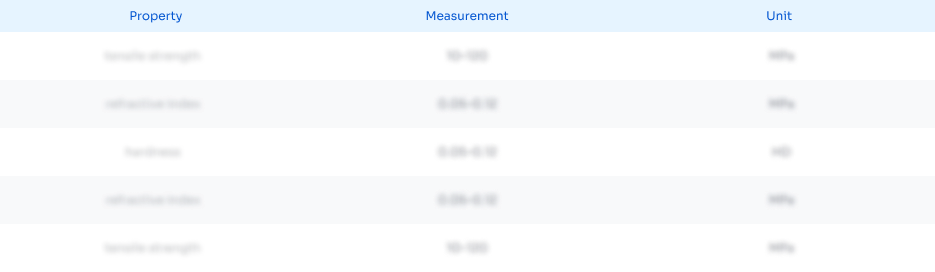
Abstract
Description
Claims
Application Information

- R&D
- Intellectual Property
- Life Sciences
- Materials
- Tech Scout
- Unparalleled Data Quality
- Higher Quality Content
- 60% Fewer Hallucinations
Browse by: Latest US Patents, China's latest patents, Technical Efficacy Thesaurus, Application Domain, Technology Topic, Popular Technical Reports.
© 2025 PatSnap. All rights reserved.Legal|Privacy policy|Modern Slavery Act Transparency Statement|Sitemap|About US| Contact US: help@patsnap.com