Low-power resistance spot-welding process adopting multi-end electrode
A terminal electrode, resistance spot welding technology, applied in resistance welding equipment, welding equipment, manufacturing tools, etc., can solve the problems of large welding penetration, unstable single-point welding, welding spatter, etc., to eliminate position changes and stabilize And the effect of high-quality resistance spot welding connection and stable position relationship
- Summary
- Abstract
- Description
- Claims
- Application Information
AI Technical Summary
Problems solved by technology
Method used
Image
Examples
Embodiment Construction
[0023] The following will clearly and completely describe the technical solutions in the embodiments of the present invention with reference to the accompanying drawings in the embodiments of the present invention. Obviously, the described embodiments are only some, not all, embodiments of the present invention. Based on the embodiments of the present invention, all other embodiments obtained by persons of ordinary skill in the art without making creative efforts belong to the protection scope of the present invention.
[0024] The invention provides a low-power multi-terminal electrode resistance spot welding welding process, which includes the following specific steps: Step S1: cleaning the welding area of the thin-walled gasket 1 and the filter screen 3, first performing mechanical polishing to remove the thin-walled gasket and After polishing the oxide film on the filter, use absolute ethanol or acetone to clean the welding area to ensure that the welding area is clean be...
PUM
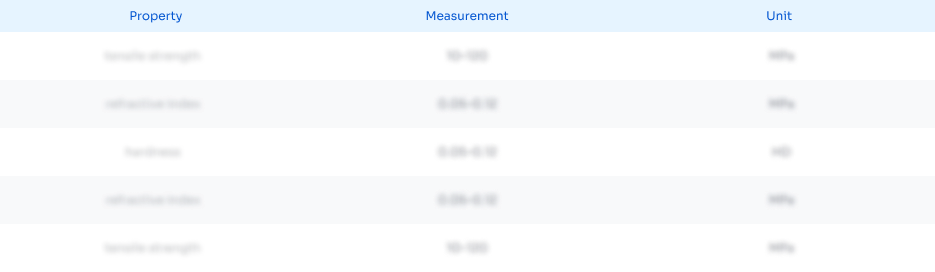
Abstract
Description
Claims
Application Information

- R&D
- Intellectual Property
- Life Sciences
- Materials
- Tech Scout
- Unparalleled Data Quality
- Higher Quality Content
- 60% Fewer Hallucinations
Browse by: Latest US Patents, China's latest patents, Technical Efficacy Thesaurus, Application Domain, Technology Topic, Popular Technical Reports.
© 2025 PatSnap. All rights reserved.Legal|Privacy policy|Modern Slavery Act Transparency Statement|Sitemap|About US| Contact US: help@patsnap.com