Device and method for testing contact stress between shield tunnel segments
A shield tunnel segment and contact stress technology, which is applied in fluid pressure measurement using piezoelectric devices, hydraulic/pneumatic force measurement, etc., can solve the problem of no longer being able to place sensors, tunnel water leakage, poor segment assembly quality, etc. problem, to achieve the effect of convenient and flexible layout and intuitive reflection
- Summary
- Abstract
- Description
- Claims
- Application Information
AI Technical Summary
Problems solved by technology
Method used
Image
Examples
Embodiment
[0038] The arrangement of sensors in this embodiment is as follows figure 1 and figure 2 As shown, when installing, insert the embedded piezoelectric sensor 1 into the gap between the segment 3, and use the air pump to pump air into the embedded piezoelectric sensor 1 from the valve 9 to ensure that the embedded piezoelectric sensor 1 and the tube Sheet 3 is in close contact and stops after leaking will not occur, and closes valve 9 to ensure sealing.
[0039] The embedded piezoelectric sensor 1 can be arranged at any position between the ring seams of the completed shield tunnel. The first ring segment is recommended to be arranged at four positions, that is, the upper, lower, left, and right positions of the shield tunnel, which can determine the distance between the three shield tunnel segments. The contact stress can also determine the attitude of the shield tunnel.
[0040] The embedded piezoelectric sensor of the present embodiment constitutes as image 3 As shown, t...
PUM
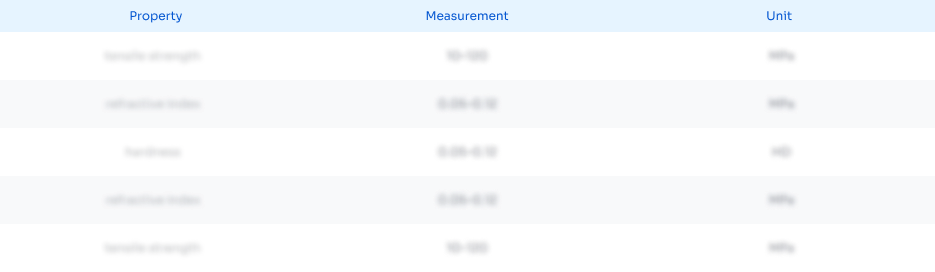
Abstract
Description
Claims
Application Information

- Generate Ideas
- Intellectual Property
- Life Sciences
- Materials
- Tech Scout
- Unparalleled Data Quality
- Higher Quality Content
- 60% Fewer Hallucinations
Browse by: Latest US Patents, China's latest patents, Technical Efficacy Thesaurus, Application Domain, Technology Topic, Popular Technical Reports.
© 2025 PatSnap. All rights reserved.Legal|Privacy policy|Modern Slavery Act Transparency Statement|Sitemap|About US| Contact US: help@patsnap.com