Sorting method for pre-enriching aggregate disseminated stibnite
A technology for distributing stibnite and aggregates, which is applied in the field of pre-enrichment of aggregates imbedded with stibnite, can solve the problem of unavoidable mixing of a large amount of surrounding rock or waste rock, low grade of antimony ore, and increased separation Other problems such as difficulty, to achieve the effect of saving mineral processing costs, not easy to slime, and reducing the amount of ore
- Summary
- Abstract
- Description
- Claims
- Application Information
AI Technical Summary
Problems solved by technology
Method used
Image
Examples
Embodiment 1
[0035] Example 1 A stibnite ore in Gansu Province has an antimony grade of 2.43%, and technological mineralogy research shows that the ore belongs to aggregate mosaic stibnite.
[0036] A sorting method for pre-enrichment of aggregate mosaic stibnite, comprising the following steps:
[0037] ⑴ Broken:
[0038] Put the aggregate-embedded stibnite raw ore into the three-stage and one-closed-circuit crushing process. First, the jaw crusher is used for two-stage coarse crushing to obtain coarse crushed products; then the coarse crushed products are screened by a 40mm vibrating screen to obtain The product on the vibrating screen and the product under the vibrating screen; the product on the vibrating screen is crushed by an impact crusher, and the crushed product is returned to the vibrating screen.
[0039] ⑵ Screening and desliming:
[0040] The product under the vibrating screen enters the desliming sieve with a mesh size of 6mm for screening and desliming to obtain the produ...
Embodiment 2
[0047] Example 2 A certain antimony ore in Hunan Province has an antimony grade of 1.96%. The ore is embedded in aggregates. At the same time, waste rocks accidentally fell into it during the mining process, resulting in a low grade of antimony ore.
[0048] A sorting method for the pre-enrichment of aggregate-embedded stibnite is the same as that in Example 1. Among them: the condition of dense medium separation means that the separation specific gravity is controlled at 2.67, the selected feed particle size is 6~40mm, the feed speed is 0.1~0.5m / s, and the separation speed is 0.11~0.26m / s. The heavy product with antimony recovery rate of 96.5% and the light product with yield of 50% were obtained by sorting.
Embodiment 3
[0049] Example 3 A stibnite in Guangxi has an antimony grade of 2.75%, and the ore is of aggregate embedded type.
[0050] A sorting method for the pre-enrichment of aggregate-embedded stibnite is the same as that in Example 1. Among them: the condition of dense medium separation means that the separation specific gravity is controlled at 2.64, the selected feed particle size is 6~40mm, the feed speed is 0.1~0.5m / s, and the separation speed is 0.11~0.26m / s. The antimony heavy product with a recovery rate of 94.6% and the light product with a yield of 48% were obtained by sorting.
PUM
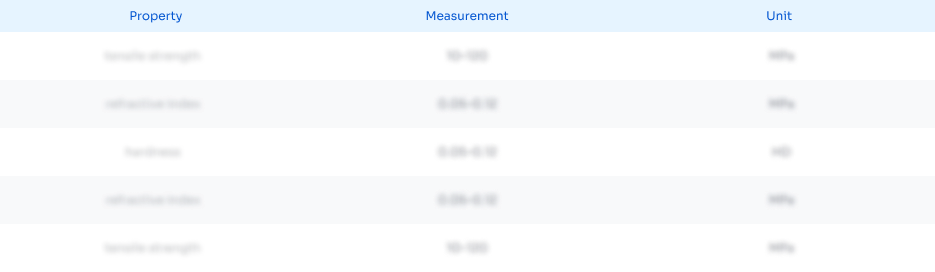
Abstract
Description
Claims
Application Information

- R&D Engineer
- R&D Manager
- IP Professional
- Industry Leading Data Capabilities
- Powerful AI technology
- Patent DNA Extraction
Browse by: Latest US Patents, China's latest patents, Technical Efficacy Thesaurus, Application Domain, Technology Topic, Popular Technical Reports.
© 2024 PatSnap. All rights reserved.Legal|Privacy policy|Modern Slavery Act Transparency Statement|Sitemap|About US| Contact US: help@patsnap.com