A kind of polyester resin powder coating
A powder coating, polyester resin technology, applied in powder coatings, polyester coatings, epoxy resin coatings, etc., can solve the problem that the impact resistance of the coating is not significantly improved, affects the appearance of the coating, and affects the graphene coating. performance and other issues, to avoid shape effects, improve impact performance, and improve stability
- Summary
- Abstract
- Description
- Claims
- Application Information
AI Technical Summary
Problems solved by technology
Method used
Image
Examples
preparation example Construction
[0032] The preparation method of described powder coating comprises the following steps:
[0033] S1: Select metal materials and prepare continuous metal fibers by cluster drawing method, and then cut the metal fibers to obtain chopped metal wires;
[0034] S2: After uniformly mixing polyester resin, epoxy resin, modifier, benzoin, and leveling agent according to a given ratio, put the mixture into a stirring tank, and fully stir the raw materials in the stirring tank;
[0035] S3: On the basis of the step S2, add a coupling agent and a curing agent to the stirred tank, and fully stir and mix to obtain a premix;
[0036] S4: On the basis of step S3, put the premixed material into the twin-screw extruder, and the extruded material is compressed and cooled to obtain a sheet material;
[0037] S5: Put the flake material into the pulverizer and pulverize it to obtain granules, and fully mix the chopped wire with the pulverized granules to obtain the finished powder coating;
[0...
Embodiment approach
[0043] As an embodiment of the present invention, after the metal wire is re-stretched under heating, the metal wire presents a wave shape;
[0044] When working, after the metal wire is restored to its original shape, the metal wire presents a wavy shape, which can improve the bonding force between the metal wire and the coating, and prevent the coating from cracking and crack gaps when the coating is impacted by external forces. There is slippage along the length direction of the metal wire, which causes the cracks in the coating to expand, which increases the damage of the coating, affects the normal use of the coating, and affects the protection effect of the coating on the workpiece.
[0045] As an embodiment of the present invention, after the metal wire is surface-treated, the metal wire is crimped into a ball; the surface treatment of the metal wire is gas-phase low-temperature plasma treatment, and the treatment time is 10-12 minutes;
[0046] When working, before the...
PUM
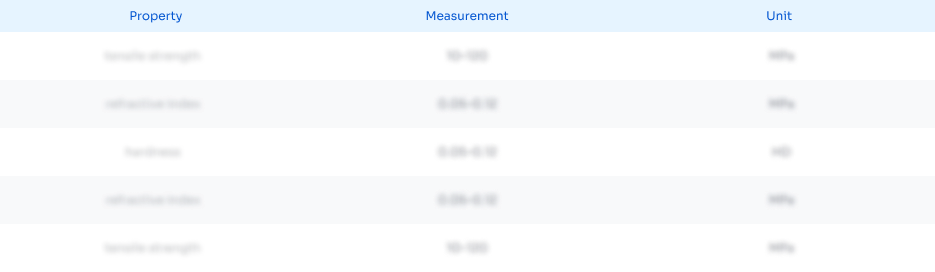
Abstract
Description
Claims
Application Information

- R&D Engineer
- R&D Manager
- IP Professional
- Industry Leading Data Capabilities
- Powerful AI technology
- Patent DNA Extraction
Browse by: Latest US Patents, China's latest patents, Technical Efficacy Thesaurus, Application Domain, Technology Topic, Popular Technical Reports.
© 2024 PatSnap. All rights reserved.Legal|Privacy policy|Modern Slavery Act Transparency Statement|Sitemap|About US| Contact US: help@patsnap.com