Bulk cement storage and recovery silo
A technology for bulk cement and recycling cylinders, applied in packaging, loading/unloading, transportation and packaging, etc., can solve the problems of poor use effect, inability to achieve zero discharge and cement recycling, etc., achieve simple structure, eliminate air pollution, use handy effect
- Summary
- Abstract
- Description
- Claims
- Application Information
AI Technical Summary
Problems solved by technology
Method used
Image
Examples
Embodiment 1
[0044] Such as Figure 1 to Figure 7 As shown, the bulk cement storage and recovery silo in this embodiment includes a cylinder body 1100, the top of the cylinder body 1100 is provided with a vent hole 1101, and the bottom of the cylinder body 1100 is provided with a discharge port 1102. The discharge port 1102 is connected to the transfer tank (not shown in the figure), and the exhaust hole 1101 is communicated with an exhaust supercharging mechanism 1200 through an exhaust pipeline 1110; the exhaust supercharging mechanism 1200 includes an exhaust pump 1210, Filter box 1220 and air compressor 1260, the air inlet of the exhaust pump 1210 is connected to the exhaust pipeline 1110, the outlet of the exhaust pump 1210 is connected to the filter box 1220, and the outlet of the filter box 1220 is connected to To the air compressor 1260 , the outlet of the air compressor 1260 is connected to the transfer tank through a one-way valve 1261 .
[0045]Through the scheme of this embodi...
Embodiment 2
[0066] Such as Figure 8 As shown, the bulk cement storage and recovery silo in this embodiment is based on the technical solutions in the above embodiments, and a transition box 1300 is fixed below the cylinder body 1100, and the bottom end of the discharge 1120 extends into the transition box In 1300, the discharge pipe 1120 is slidingly connected to the transition box 1300, and the transition box 1300 is connected to the transfer tank.
[0067] In the absence of the transition box 1300, the discharge pipe 1120 is directly connected to the transfer tank through a hose. In actual use, the efficiency of the hose will be reduced due to bending, and the left and right shaking of the hose will also be damaged due to friction. Therefore, after the transition box 1300 is adopted, the transfer tank and the transition box 1300 can be connected by hard pipes, and the cement is directly pumped into the transition box 1300, and then is pumped into the discharge pipe 1120 through the tra...
PUM
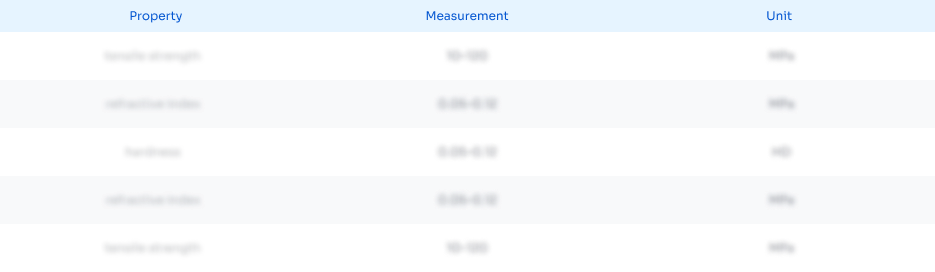
Abstract
Description
Claims
Application Information

- R&D
- Intellectual Property
- Life Sciences
- Materials
- Tech Scout
- Unparalleled Data Quality
- Higher Quality Content
- 60% Fewer Hallucinations
Browse by: Latest US Patents, China's latest patents, Technical Efficacy Thesaurus, Application Domain, Technology Topic, Popular Technical Reports.
© 2025 PatSnap. All rights reserved.Legal|Privacy policy|Modern Slavery Act Transparency Statement|Sitemap|About US| Contact US: help@patsnap.com