Energy-saving optimization method for integration of melting, distribution and heat preservation parameters for aluminum die casting
An optimization method, aluminum die-casting technology, applied in design optimization/simulation, energy industry, data processing applications, etc., can solve problems such as large transportation intervals, waste, high heat preservation energy consumption, etc., and achieve the goal of reducing workload and production costs Effect
- Summary
- Abstract
- Description
- Claims
- Application Information
AI Technical Summary
Problems solved by technology
Method used
Image
Examples
Embodiment Construction
[0053] In order to describe the present invention more specifically, the technical solutions of the present invention will be described in detail below in conjunction with the accompanying drawings and specific embodiments.
[0054] The present invention is an energy-saving optimization method for the integration of melting, distribution and heat preservation parameters of aluminum die-casting, which includes the following steps:
[0055] (1) The pouring quality Mp of each holding furnace for the corresponding die-casting machine in a whole composed of a melting furnace (melting furnace number is n) and multiple holding furnaces (holding furnace number is k) k , the interval time Tp of each pouring k , The number of products Qp that each die-casting machine needs to produce k , The heat preservation amount Mms of the melting furnace at the initial moment n , The state Ssims of the melting burner at the initial moment of the melting furnace n (0 stands for standby, 1 stands ...
PUM
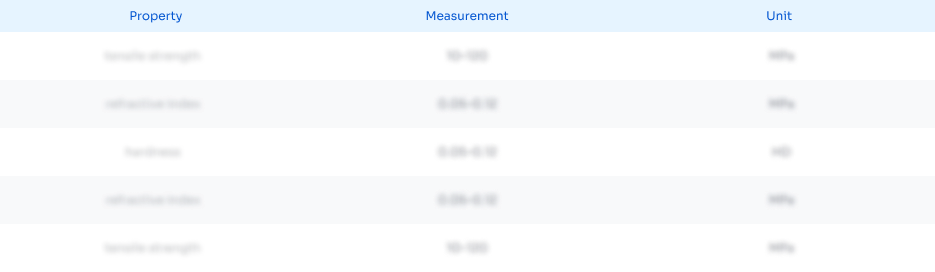
Abstract
Description
Claims
Application Information

- R&D Engineer
- R&D Manager
- IP Professional
- Industry Leading Data Capabilities
- Powerful AI technology
- Patent DNA Extraction
Browse by: Latest US Patents, China's latest patents, Technical Efficacy Thesaurus, Application Domain, Technology Topic, Popular Technical Reports.
© 2024 PatSnap. All rights reserved.Legal|Privacy policy|Modern Slavery Act Transparency Statement|Sitemap|About US| Contact US: help@patsnap.com