Rinsing system and rinsing method for cold-rolled strip steel pickling
A steel pickling and rinsing technology, which is applied in the field of cold-rolled strip pickling rinsing systems, can solve the problems of increasing the number of equipment, maintenance workload, and increasing floor space, so as to reduce usage, reduce carry-out, and free The effect of acid content reduction
- Summary
- Abstract
- Description
- Claims
- Application Information
AI Technical Summary
Problems solved by technology
Method used
Image
Examples
Embodiment 1
[0054] figure 1 A schematic diagram of a cold-rolled strip pickling rinsing system according to an embodiment of the present invention is shown.
[0055] Such as figure 1 As shown, this embodiment provides a rinsing system for pickling cold-rolled steel strips. The rinsing system includes a first rinsing tank 1, a second rinsing tank 2, a third rinsing tank 3 and a fourth rinsing tank arranged adjacently in sequence. 4. No. 1 squeeze roller 5 and No. 5 squeeze roller 9 are installed at both ends of the four rinsing tanks, and No. 2 squeeze roller 6, No. 3 squeeze roller 7 and No. Dry roller 8, each rinsing tank is provided with a suction port, the rinsing tank is connected to the circulation pump through the suction port, the first rinsing tank 1, the second rinsing tank 2, the third rinsing tank 3 and the fourth rinsing tank 4 Respectively connect the first circulating pump 10, the second circulating pump 11, the third circulating pump 12 and the fourth circulating pump 13,...
Embodiment 2
[0096] image 3 A schematic flow chart of a cold-rolled strip pickling and rinsing method according to an embodiment of the present invention is shown.
[0097] Such as image 3 As shown, the present embodiment provides a kind of rinsing method of cold-rolled strip pickling, utilizes the rinsing system of cold-rolled strip pickling in embodiment 1 to carry out rinsing, and this rinsing method comprises the steps:
[0098] Step 1, rinse water is now provided in the first rinse tank, the second rinse tank, the third rinse tank and the fourth rinse tank;
[0099] Step 2, the strip passes through the No. 1 squeeze roll, the first rinse tank, the No. 2 squeeze roll, the second rinse tank, the No. 3 squeeze roll, the third rinse tank, the No. 4 squeeze roll, and the fourth rinse tank and No. 5 squeeze roller;
[0100] In step 3, the steel strip on each rinsing tank is cleaned twice through the three spray pipes connected to the rinsing water of this rinsing tank and the double sp...
PUM
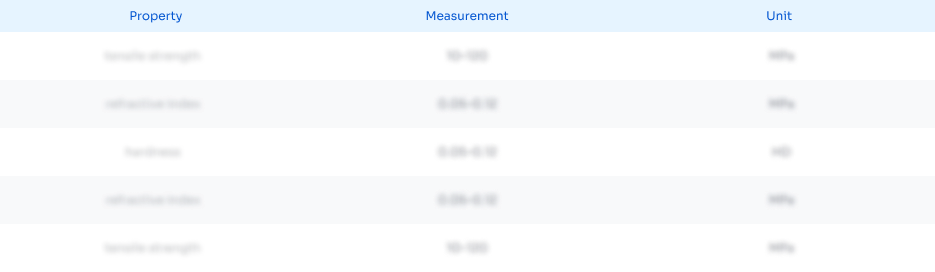
Abstract
Description
Claims
Application Information

- Generate Ideas
- Intellectual Property
- Life Sciences
- Materials
- Tech Scout
- Unparalleled Data Quality
- Higher Quality Content
- 60% Fewer Hallucinations
Browse by: Latest US Patents, China's latest patents, Technical Efficacy Thesaurus, Application Domain, Technology Topic, Popular Technical Reports.
© 2025 PatSnap. All rights reserved.Legal|Privacy policy|Modern Slavery Act Transparency Statement|Sitemap|About US| Contact US: help@patsnap.com