Robot trajectory planning method and system for ingot repairing process
A technology of trajectory planning and robotics, applied in the direction of program control manipulators, manipulators, manufacturing tools, etc., can solve problems such as difficult non-ferrous metal ingot repair, difficult to plan trajectory, dimension disaster, etc., to achieve the effect of reducing computational complexity
- Summary
- Abstract
- Description
- Claims
- Application Information
AI Technical Summary
Problems solved by technology
Method used
Image
Examples
Embodiment 1
[0029] Such as figure 1 As shown, a robot trajectory planning method, including:
[0030] Obtain a given path, introduce path parameters, and parametrically represent the Cartesian coordinates of the given path;
[0031] Map the parameterized Cartesian coordinates of the path to the joint position, velocity and acceleration of the robot; select a three-segment path acceleration trajectory or its improved path acceleration trajectory to obtain the expression of the path parameters and their derivatives; use the parameterized Joint variables, velocities and accelerations parameterize the robot kinematics and dynamics equations and obtain performance index functions;
[0032] According to the performance index function, the optimization algorithm is used to solve the optimal parameters of the path acceleration trajectory, and the robot trajectory along the given path under the optimal parameters is obtained.
[0033] Specifically, the path acceleration trajectory is a three-seg...
Embodiment 2
[0081] A robot trajectory planning system, comprising:
[0082] The data collection module is configured to obtain a given path, introduce path parameters, and parametrically represent the Cartesian coordinates of the given path;
[0083] The data processing module is configured to map the parameterized Cartesian coordinates of the path to the joint position, velocity and acceleration of the robot; select a three-segment path acceleration trajectory or an improved path acceleration trajectory to obtain the path parameters and their derivatives Expression; use parameterized joint variables, speed and acceleration to parameterize robot kinematics and dynamics equations, and obtain performance index functions;
[0084] The optimal parameter determination module is configured to use an optimization algorithm to solve the optimal parameters of the path acceleration trajectory according to the performance index function, and obtain the robot trajectory along the given path under the...
Embodiment 3
[0087] A computer-readable storage medium is used for storing computer instructions. When the computer instructions are executed by a processor, the robot trajectory planning method described in the above-mentioned embodiments is completed.
PUM
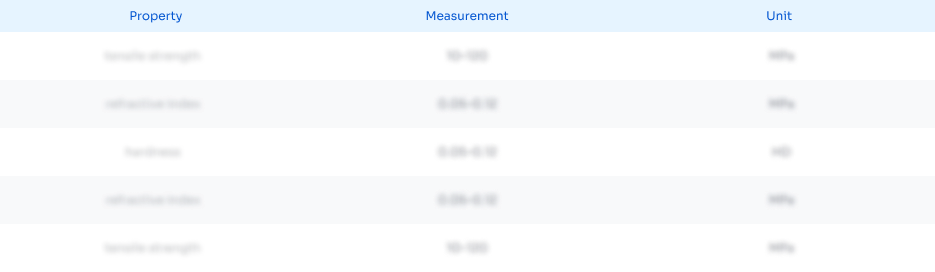
Abstract
Description
Claims
Application Information

- R&D
- Intellectual Property
- Life Sciences
- Materials
- Tech Scout
- Unparalleled Data Quality
- Higher Quality Content
- 60% Fewer Hallucinations
Browse by: Latest US Patents, China's latest patents, Technical Efficacy Thesaurus, Application Domain, Technology Topic, Popular Technical Reports.
© 2025 PatSnap. All rights reserved.Legal|Privacy policy|Modern Slavery Act Transparency Statement|Sitemap|About US| Contact US: help@patsnap.com