Aviation spur gear shape modification method based on dynamic simulation
A dynamic simulation, spur gear technology, applied in design optimization/simulation, special data processing applications, instruments, etc., can solve problems such as abnormal contact marks, abnormal wear, eccentric load, etc., to improve working life and improve abnormal contact problems. Effect
- Summary
- Abstract
- Description
- Claims
- Application Information
AI Technical Summary
Problems solved by technology
Method used
Image
Examples
Embodiment
[0063] An aviation high-speed heavy-duty spur gear, its gear parameters are as follows: the number of teeth of the driving wheel is 24, the number of teeth of the driven wheel is 38, the modulus is 3, the pressure angle is 25°, the tooth width of the driving wheel is 18.5mm, the diameter of the addendum circle is 78mm, and the diameter of the root circle is 64.8mm mm, inner hole diameter 35mm, top fillet R0.5, root circle R1.05, backlash 0.08mm, tooth surface roughness 0.32. Driven wheel tooth width 22.5mm, addendum circle diameter 120mm, dedendum circle diameter 106.8mm, inner hole diameter 42mm, addendum fillet R0.5, dedendum circle R1.05, tooth side clearance 0.08mm, tooth surface roughness 0.32 . The gear material is 16Cr3NiWMoVNbE, the transmission power is 370.56KW, the driving gear speed is 9280r / min, and the driven gear speed is 5861r / min.
[0064] 1. Use KISSSoft software to carry out detailed three-dimensional modeling of gears according to gear parameters.
[0065...
PUM
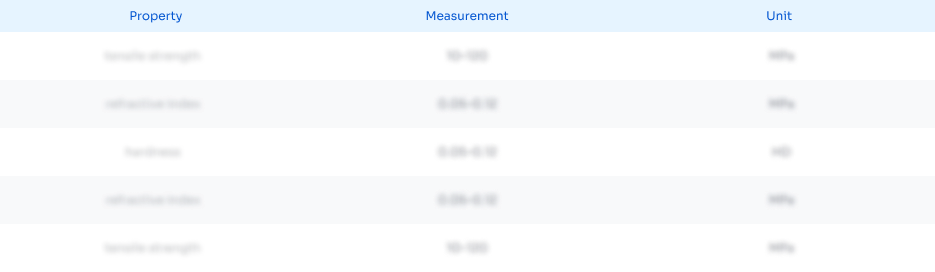
Abstract
Description
Claims
Application Information

- R&D
- Intellectual Property
- Life Sciences
- Materials
- Tech Scout
- Unparalleled Data Quality
- Higher Quality Content
- 60% Fewer Hallucinations
Browse by: Latest US Patents, China's latest patents, Technical Efficacy Thesaurus, Application Domain, Technology Topic, Popular Technical Reports.
© 2025 PatSnap. All rights reserved.Legal|Privacy policy|Modern Slavery Act Transparency Statement|Sitemap|About US| Contact US: help@patsnap.com