An Accurate Design Method of Shrinkage Dimensions of Castings Based on Local Envelope Density
A design method, casting shrinkage technology, applied in constraint-based CAD, design optimization/simulation, geometric CAD, etc., can solve the problems of large dimensional accuracy errors and insignificant accuracy effects of castings, and achieve the solution of large accuracy errors and design methods Reasonable, feasible and operable
- Summary
- Abstract
- Description
- Claims
- Application Information
AI Technical Summary
Problems solved by technology
Method used
Image
Examples
specific Embodiment approach 1
[0020] Specific Embodiment 1: In this embodiment, an accurate design method of casting shrinkage size based on local envelope density is completed according to the following steps:
[0021] 1. Divide the test model into several local envelopes according to the contraction center ray division method, first calculate the local envelope density of any local envelope, and according to the quadratic relationship curve between the local envelope density and the shrinkage rate, get Calculate the shrinkage of the local envelope, and then use the same method to obtain the shrinkage of all the local envelopes of the test model;
[0022] 2. Convert the shrinkage rate of all local envelopes of the test model into the shrinkage rate of the same part on the casting. The conversion formula is as follows:
[0023] ε li = α 1 ·ε 1 +α 2 ·ε 2 +…+α n ·ε n +(1-α 1 -α 2 -...-α n )·ε 0
[0024] In the formula, ε n Represents the shrinkage rate of the nth local envelope of the test model...
specific Embodiment approach 2
[0028] Specific embodiment two: the difference between this embodiment and specific embodiment one is: the shrinkage center ray division method described in step one includes the following steps: first determine the shrinkage center of the test model and the envelope of the test model, and then from the shrinkage Make several rays from the center to the envelope of the test model, and the closed space formed by two adjacent rays and the edge of the envelope is a local envelope.
[0029] Other steps are the same as in the first embodiment.
specific Embodiment approach 3
[0030] Embodiment 3: The difference between this embodiment and Embodiment 1 or 2 is that the contraction center of the test model is the center of mass of the test model.
[0031] Other steps are the same as those in Embodiment 1 or 2.
PUM
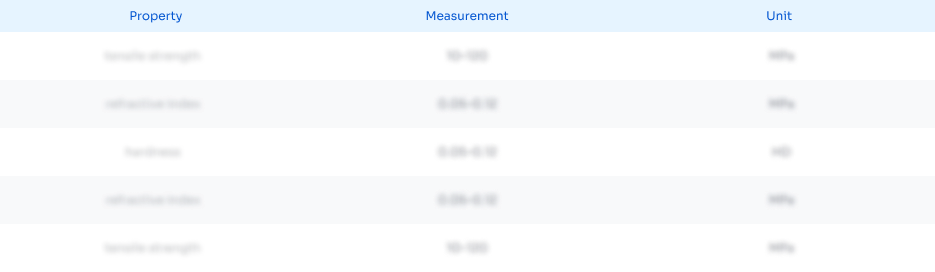
Abstract
Description
Claims
Application Information

- R&D
- Intellectual Property
- Life Sciences
- Materials
- Tech Scout
- Unparalleled Data Quality
- Higher Quality Content
- 60% Fewer Hallucinations
Browse by: Latest US Patents, China's latest patents, Technical Efficacy Thesaurus, Application Domain, Technology Topic, Popular Technical Reports.
© 2025 PatSnap. All rights reserved.Legal|Privacy policy|Modern Slavery Act Transparency Statement|Sitemap|About US| Contact US: help@patsnap.com