Special alloy pre-reactor plate spring transmission shaft structure
A technology of pre-reactor and transmission shaft, applied in the direction of shaft, bearing element, shaft and bearing, etc., can solve the problems of small elasticity and leakage of O-ring
- Summary
- Abstract
- Description
- Claims
- Application Information
AI Technical Summary
Problems solved by technology
Method used
Image
Examples
Embodiment Construction
[0016] The present invention will be described in detail below in conjunction with the accompanying drawings. As shown in the figure, a special alloy pre-reactor plate spring transmission shaft structure includes a transmission shaft 7. The end of the transmission shaft is provided with a shoulder 71, which abuts against the shaft shoulder. The threaded section of the thread retaining ring 1 is screwed with the adjusting nut 2, and the inner side of the end of the adjusting nut is provided with a spring seat 4, and the spring seat is provided with a boss 41, and the shape of the boss and the end of the adjusting nut are complementary and Fastened together, the disc spring group 3 set on the transmission shaft is set between the threaded retaining ring 1 and the spring seat 4, and the two ends of the disc spring group respectively abut against the threaded retaining ring and the spring seat; The foundation seat 8 connected on the transmission shaft also abuts against the other s...
PUM
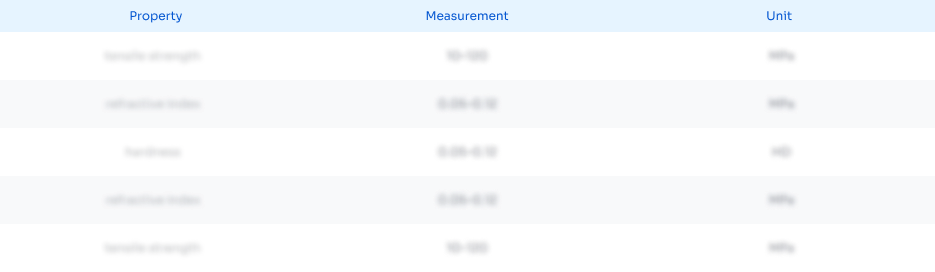
Abstract
Description
Claims
Application Information

- R&D Engineer
- R&D Manager
- IP Professional
- Industry Leading Data Capabilities
- Powerful AI technology
- Patent DNA Extraction
Browse by: Latest US Patents, China's latest patents, Technical Efficacy Thesaurus, Application Domain, Technology Topic, Popular Technical Reports.
© 2024 PatSnap. All rights reserved.Legal|Privacy policy|Modern Slavery Act Transparency Statement|Sitemap|About US| Contact US: help@patsnap.com