Construction process for shaping needle-sheet-shaped gravel
A construction technique and needle flake technology, which is applied in grain processing, etc., can solve the problems of production decline and needle flake content exceeding the standard, and achieve the effect of increasing yield
- Summary
- Abstract
- Description
- Claims
- Application Information
AI Technical Summary
Problems solved by technology
Method used
Image
Examples
Embodiment Construction
[0026] The technical solution of the present invention is further described below, but the scope of protection is not limited to the description.
[0027] see Figure 1 to Figure 4 shown.
[0028] A kind of crusher for shaping needle flake sandstone of the present invention, comprises: casing cover 1, shaping rolling body 2, the rotatable gap of shaping rolling body 2 is installed in the hollow interior of casing cover 1, and casing cover 1. A plurality of spaced crushing grooves 11 are arranged on the side wall;
[0029] After crushing, the needle-shaped sandstone is brought into the shaping chute 21 on the rotating shaping roller body 2 for spiral rotation, and the finely crushed sandstone falls from the gap between the shaping roller body 2 and the casing cover 1, The elongated needle-shaped sandstone enters the shaping chute 21 and is crushed and shaped for the first time. After elastic deformation and shaping, the needle-shaped sandstone enters the shaping chute 21 and ...
PUM
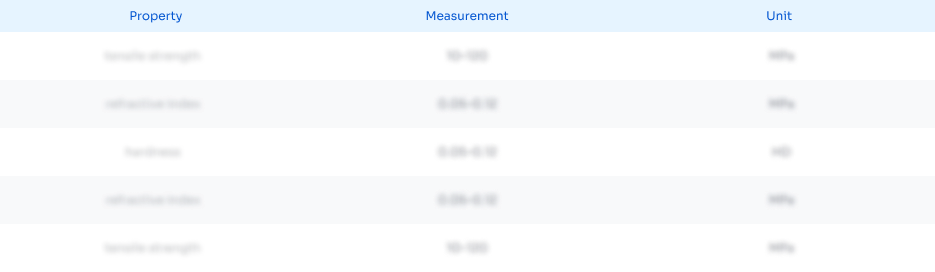
Abstract
Description
Claims
Application Information

- R&D Engineer
- R&D Manager
- IP Professional
- Industry Leading Data Capabilities
- Powerful AI technology
- Patent DNA Extraction
Browse by: Latest US Patents, China's latest patents, Technical Efficacy Thesaurus, Application Domain, Technology Topic, Popular Technical Reports.
© 2024 PatSnap. All rights reserved.Legal|Privacy policy|Modern Slavery Act Transparency Statement|Sitemap|About US| Contact US: help@patsnap.com