Hollow fiber membrane continuous production forming equipment
A technology for forming equipment and fiber membranes, which is applied in the field of continuous production and forming equipment for hollow fiber membranes, can solve the problems of increasing the work flow of operators, inconvenience, and difficult to remove, so as to improve the drying effect, improve the cleaning efficiency, and improve the fit. Effect
- Summary
- Abstract
- Description
- Claims
- Application Information
AI Technical Summary
Problems solved by technology
Method used
Image
Examples
Embodiment 1
[0046] Example 1, such as Figure 3-4 As shown, before the film thread is pressed, the pulley A4 can be driven to rotate by the start of the servo motor 402, and the connection between the belt 401 and the pulley B409 can cause the pulley B409 to drive the internal thread sleeve 407 to rotate, and the rotation of the internal thread sleeve 407 can be used Drive the threaded column 408 to push the connecting frame 406 up and down as a whole under the limit sliding of the slider 4010 and the chute 404, so that the connecting frame 406 drives the pressure roller B405 and the pressure roller A403 to move closer to each other, and then adjust the distance between the pressure roller A403 and the pressure roller B405. The pressing distance is adapted to different types of membrane filaments, increasing the convenience and operability of pressing adjustment work.
Embodiment 2
[0047] Example 2, such as Figure 5 As shown, when the film filament enters the drying chamber 154, the gear 151 is driven to rotate by the start of the biaxial motor 15, and the meshing and matching between the gear 151 and the outer ring gear 152 is used to promote the outer ring gear 152 to drive the drying chamber 154 as a whole. The guidance of the guide groove 153 cooperates with the centrifugal rotation. During this period, the drying of the membrane yarn is carried out with the start of the hot air blower 156. At the same time, the oblique guide structure of the trapezoidal block 155 is used to make the drying air quickly spread to both sides and improve the drying of the membrane yarn. Dry the effect, and flow the water flowing down from the membrane filaments to both sides, cooperate with the centrifugal rotation of the drying chamber 154 to brush off the water liquid, and promote the drying of the water liquid to form gas, so as to enhance the drying efficiency and e...
PUM
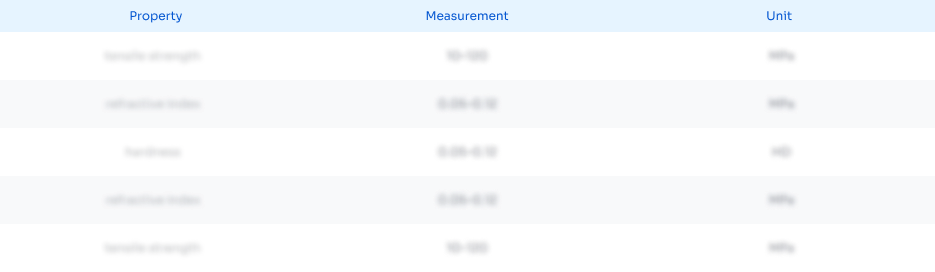
Abstract
Description
Claims
Application Information

- R&D
- Intellectual Property
- Life Sciences
- Materials
- Tech Scout
- Unparalleled Data Quality
- Higher Quality Content
- 60% Fewer Hallucinations
Browse by: Latest US Patents, China's latest patents, Technical Efficacy Thesaurus, Application Domain, Technology Topic, Popular Technical Reports.
© 2025 PatSnap. All rights reserved.Legal|Privacy policy|Modern Slavery Act Transparency Statement|Sitemap|About US| Contact US: help@patsnap.com