Reflective film continuous processing production device based on base material embossing and processing method thereof
A production device and technology for reflective film, applied in the direction of lamination device, chemical instrument and method, lamination, etc., can solve the problem of affecting the processing efficiency of reflective film, inability to clean, and the lamination of the first substrate and the second substrate. shift problem
- Summary
- Abstract
- Description
- Claims
- Application Information
AI Technical Summary
Problems solved by technology
Method used
Image
Examples
Embodiment Construction
[0033] The following will clearly and completely describe the technical solutions in the embodiments of the present invention with reference to the accompanying drawings in the embodiments of the present invention. Obviously, the described embodiments are only some, not all, embodiments of the present invention. Based on the embodiments of the present invention, all other embodiments obtained by persons of ordinary skill in the art without making creative efforts belong to the protection scope of the present invention.
[0034] see Figure 1-7 , the present invention provides a technical solution: a continuous processing and production device for reflective film based on substrate embossing, including a processing table 1, a first feed roller 2 is fixedly installed on the top side of the processing table 1, and the processing table 1 A second feed roller 3 is fixedly installed on the side close to the first feed roller 2 at the top, and a positioning cleaning mechanism 4 is fi...
PUM
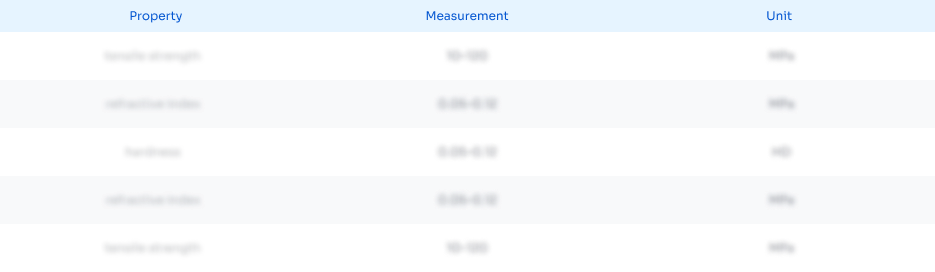
Abstract
Description
Claims
Application Information

- R&D Engineer
- R&D Manager
- IP Professional
- Industry Leading Data Capabilities
- Powerful AI technology
- Patent DNA Extraction
Browse by: Latest US Patents, China's latest patents, Technical Efficacy Thesaurus, Application Domain, Technology Topic, Popular Technical Reports.
© 2024 PatSnap. All rights reserved.Legal|Privacy policy|Modern Slavery Act Transparency Statement|Sitemap|About US| Contact US: help@patsnap.com