Mechanical arm target tracking method based on visual servo
A technology of visual servoing and manipulators, applied in manipulators, program-controlled manipulators, comprehensive factory control, etc., can solve the problems of large time consumption of SVM algorithm, lack of real-time performance, and deviation of accurate value of Jacobian matrix calculation, etc., to achieve improvement The effect of dynamic tracking ability and speed stability, simple principle
- Summary
- Abstract
- Description
- Claims
- Application Information
AI Technical Summary
Problems solved by technology
Method used
Image
Examples
Embodiment Construction
[0059] In order to make the technical solutions and advantages of the present invention clearer, the implementation manners of the present invention will be further described in detail below in conjunction with the accompanying drawings.
[0060] One embodiment of the present invention provides a visual servo-based robotic arm target tracking method, such as figure 1 shown, including the following steps:
[0061] In the image recognition cycle, the image acquisition and feature recognition module uses the industrial camera to collect the image features of the target in real time, and detects the image feature coordinate information;
[0062] The visual servo operation module performs online estimation of the image Jacobian matrix according to the image feature coordinate information, and calculates the spatial velocity at the end of the mechanical arm at the current moment;
[0063] The manipulator motion controller module converts the space velocity at the end of the manipul...
PUM
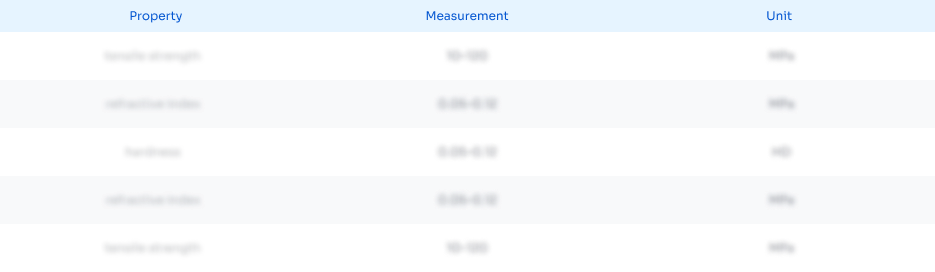
Abstract
Description
Claims
Application Information

- R&D Engineer
- R&D Manager
- IP Professional
- Industry Leading Data Capabilities
- Powerful AI technology
- Patent DNA Extraction
Browse by: Latest US Patents, China's latest patents, Technical Efficacy Thesaurus, Application Domain, Technology Topic, Popular Technical Reports.
© 2024 PatSnap. All rights reserved.Legal|Privacy policy|Modern Slavery Act Transparency Statement|Sitemap|About US| Contact US: help@patsnap.com