Method for determining dispersion coefficient of theoretical value of aircraft structure crack propagation life
A technology of crack growth life and dispersion coefficient, applied in the field of aviation fatigue fracture, which can solve problems such as differences in crack growth life test values, unstable manufacturing process methods of structural parts, and unstable material properties.
- Summary
- Abstract
- Description
- Claims
- Application Information
AI Technical Summary
Problems solved by technology
Method used
Image
Examples
specific Embodiment
[0066] The specific implementation of the method for determining the dispersion coefficient of the theoretical value of the crack growth life of the aircraft structure provided by the embodiment of the present invention will be further described in detail below with a specific embodiment.
[0067] The method for determining the dispersion coefficient of the theoretical value of the aircraft structure crack extension life based on the test provided by this specific embodiment is implemented as follows:
[0068] It is known that the crack growth trajectory and extended life of the fatigue damage tolerance test piece of an aircraft structure, the material of the test piece is 7050, and the stress ratio R=0.06.
[0069] The test-based method for determining the dispersion coefficient of the theoretical value of the aircraft structure crack growth life provided by the specific embodiment includes the following steps:
[0070] Step 1. Accurately measure the coordinates (x i ,y i )...
PUM
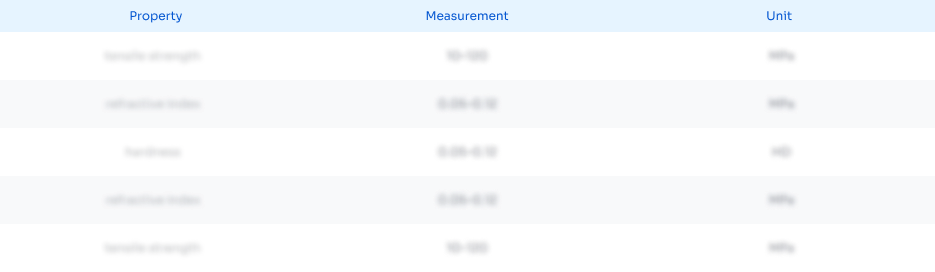
Abstract
Description
Claims
Application Information

- Generate Ideas
- Intellectual Property
- Life Sciences
- Materials
- Tech Scout
- Unparalleled Data Quality
- Higher Quality Content
- 60% Fewer Hallucinations
Browse by: Latest US Patents, China's latest patents, Technical Efficacy Thesaurus, Application Domain, Technology Topic, Popular Technical Reports.
© 2025 PatSnap. All rights reserved.Legal|Privacy policy|Modern Slavery Act Transparency Statement|Sitemap|About US| Contact US: help@patsnap.com