Composite material plate cutting device
A cutting device and composite material technology, applied in metal processing and other directions, can solve the problems of low cutting accuracy and increasing processing time.
- Summary
- Abstract
- Description
- Claims
- Application Information
AI Technical Summary
Problems solved by technology
Method used
Image
Examples
Embodiment 1
[0024] A composite material sheet cutting device, such as Figure 1-Figure 6 As shown, it includes a support foot 1, a worktable 2, a transmission mechanism 3 and a cutting mechanism 4. The top of the support foot 1 is provided with a workbench 2, the bottom of the workbench 2 is provided with a transmission mechanism 3, and the rear side of the bottom of the workbench 2 is provided with a cutting mechanism. Mechanism 4, transmission mechanism 3 cooperates with cutting mechanism 4.
[0025] When people need to cut the composite material board, people manually place the composite material board on the workbench 2, start the transmission mechanism 3, and drive the cutting mechanism 4 under the action of the transmission mechanism 3 to cut the composite material board.
[0026] The transmission mechanism 3 includes a first support block 30, a pulley set 31, a rotating shaft 32, a gear set 33 and a motor 34. Rotating shaft 32 is arranged, and belt pulley group 31 is arranged betw...
PUM
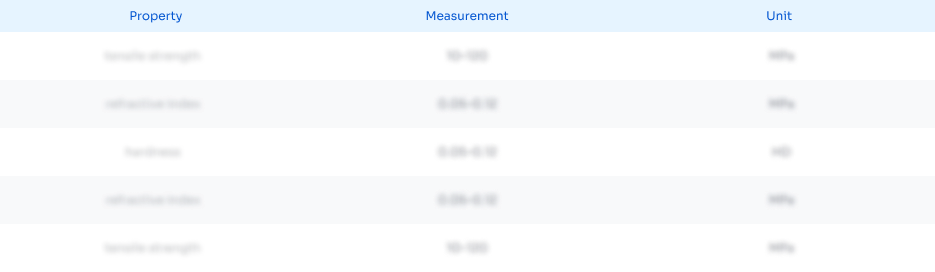
Abstract
Description
Claims
Application Information

- R&D Engineer
- R&D Manager
- IP Professional
- Industry Leading Data Capabilities
- Powerful AI technology
- Patent DNA Extraction
Browse by: Latest US Patents, China's latest patents, Technical Efficacy Thesaurus, Application Domain, Technology Topic, Popular Technical Reports.
© 2024 PatSnap. All rights reserved.Legal|Privacy policy|Modern Slavery Act Transparency Statement|Sitemap|About US| Contact US: help@patsnap.com