Endoscope optical system
An optical system and endoscope technology, applied in the field of endoscopy, can solve the problems of inability to match high-pixel large-size CMOS image sensors, inability to match image sensors, etc.
- Summary
- Abstract
- Description
- Claims
- Application Information
AI Technical Summary
Problems solved by technology
Method used
Image
Examples
Embodiment 1
[0079] see Figure 3-Figure 6 , represents the state when the second lens group 200 moves to the object side, that is, the farthest point observation state, and the state when the second lens group 200 moves to the image plane side, that is, the closest point observation state, based on the above-mentioned second lens group 200 status,
[0080] For details, refer to the data in Table 1, Table 2, and Table 3, which are the parameters and test results of specific experimental tests in this example.
[0081] Table 1
[0082] Numbering radius thickness Refractive index Abbe number SO Infinity 15.000 1 Infinity 0.300 1.883 40.87 2 1.291 0.772 3 6.106 0.525 1.850 30.06 4 Infinity 0.100 5 1.310 0.705 1.487 70.42 6 1.948 1.139 stop Infinity 0.050 8 1.870 1.040 1.618 63.41 9 -0.882 0.300 1.620 36.35 10 -2.339 0.145 11 3.896 0.558 1.618 63.41 12 Infi...
Embodiment 2
[0089] see Figure 7-Figure 10 , represents the state when the second lens group 200 moves to the object side, that is, the farthest point observation state, and the state when the second lens group 200 moves to the image plane side, that is, the closest point observation state, based on the above-mentioned second lens group 200 status.
[0090] Specifically refer to the data in Table 4, Table 5, and Table 6, which are the parameters and test results of specific experimental tests in this example.
[0091] Table 4
[0092]
[0093]
[0094] table 5
[0095] Farthest point observation state Closest observation status do 15.000 3.900 D4 0.100 0.866 D6 1.332 0.566 Half field angle (°) 72.0 71.6 Fno 7.5 7.6
[0096] Table 6
[0097] Conditional value θ 35.8 |f1 / f3| 1.30 |f1 / ft| 1.67 TT / IH 5.07 d / ft 0.50
Embodiment 3
[0099] see Figure 11-Figure 14 , represents the state when the second lens group 200 moves to the object side, that is, the farthest point observation state, and the state when the second lens group 200 moves to the image plane side, that is, the closest point observation state, based on the above-mentioned second lens group 200 status.
[0100] Specifically refer to the data in Table 7, Table 8, and Table 9, which are the parameters and test results of specific experimental tests in this example.
[0101] Table 7
[0102] Numbering radius thickness Refractive index Abbe number SO Infinity 18.000 1 Infinity 0.300 1.883 40.87 2 1.556 0.877 3 5.459 0.610 1.904 31.32 4 Infinity 0.100 5 1.519 0.654 1.487 70.42 6 2.243 1.240 stop Infinity 0.231 8 1.961 0.856 1.618 63.41 9 -1.121 0.300 1.673 32.18 10 -2.738 0.215 11 2.909 0.616 1.618 63.41 12 In...
PUM
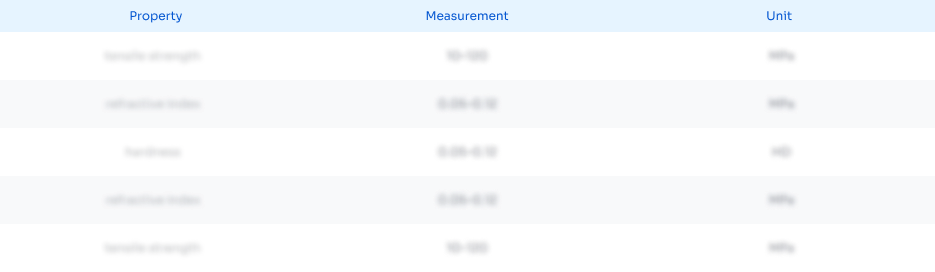
Abstract
Description
Claims
Application Information

- Generate Ideas
- Intellectual Property
- Life Sciences
- Materials
- Tech Scout
- Unparalleled Data Quality
- Higher Quality Content
- 60% Fewer Hallucinations
Browse by: Latest US Patents, China's latest patents, Technical Efficacy Thesaurus, Application Domain, Technology Topic, Popular Technical Reports.
© 2025 PatSnap. All rights reserved.Legal|Privacy policy|Modern Slavery Act Transparency Statement|Sitemap|About US| Contact US: help@patsnap.com