Material conveying gas exhaust mechanism and working method thereof
A technology of exhaust mechanism and screw conveyor, which is applied in the direction of conveyor, conveying bulk materials, transportation and packaging, etc., can solve the problems of unachievable gas discharge and inclusion of gas components.
- Summary
- Abstract
- Description
- Claims
- Application Information
AI Technical Summary
Problems solved by technology
Method used
Image
Examples
Embodiment 1
[0028] Such as figure 1 and 2 As shown, a kind of material conveying exhaust mechanism comprises mixing bucket 1 and screw conveyor 2 connected and communicated with the outlet of mixing bucket 1; One side of described mixing bucket 1 is provided with exhaust bin 3, and described The side of the screw conveyor 2 away from the discharge port is provided with an air release port 301, and the exhaust bin 3 is connected and communicated with the air release port 301; wherein the gas-powder mixture stirred by the mixing barrel 1 is separated by the screw conveyor 2 The airflow and powder are formed, the airflow is discharged into the exhaust bin 3 through the air leakage port 301, and the powder is discharged from the discharge port through the screw conveyor 2.
[0029] This kind of material conveying exhaust mechanism has the following beneficial effects: through the setting of the mixing tank 1, the stirring of the powder is promoted; through the setting of the screw conveyor 2...
Embodiment 2
[0041] Such as image 3 As shown, the second embodiment is carried out on the basis of the first embodiment, and the difference between the second embodiment and the first embodiment is that the exhaust bin 3 is arranged around the mixing tank 1, and the gas discharge port 301 is connected to the feeding port of the mixing tank 1 set up.
[0042] The advantage of this scheme is that when the hot air is discharged, part of it will stay in the exhaust chamber 3, and the exhaust chamber 3 is arranged around the mixing bucket 1, thus forming an insulation layer, and the return of the hot air can also It can hinder the discharge of very little entrained powder and ensure its overall good separation and heat preservation effect.
Embodiment 3
[0044] Embodiment three is carried out on the basis of embodiment one.
[0045] A working method of a material conveying exhaust mechanism, the mixing tank 1 stirs the gas-powder mixture and the screw conveyor 2 separates the gas and powder.
[0046] The separated gas is discharged into the exhaust bin 3 along the gas release port 301 ; the separated powder is discharged from the discharge port along the conveying direction of the screw conveyor 2 .
[0047] The working method of the material conveying exhaust mechanism has the following beneficial effects: the stirring effect is good, the powder material is evenly stirred, the quality of the discharged powder is good, and the amount of mixed gas is small.
PUM
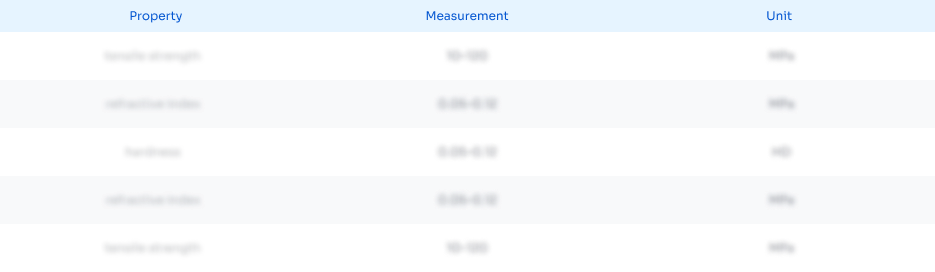
Abstract
Description
Claims
Application Information

- R&D Engineer
- R&D Manager
- IP Professional
- Industry Leading Data Capabilities
- Powerful AI technology
- Patent DNA Extraction
Browse by: Latest US Patents, China's latest patents, Technical Efficacy Thesaurus, Application Domain, Technology Topic, Popular Technical Reports.
© 2024 PatSnap. All rights reserved.Legal|Privacy policy|Modern Slavery Act Transparency Statement|Sitemap|About US| Contact US: help@patsnap.com